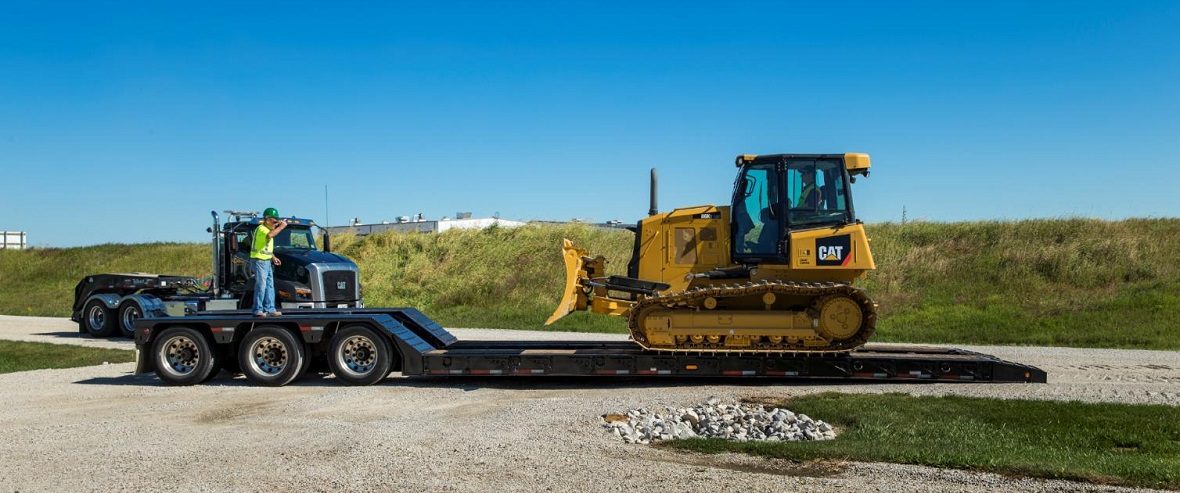
Construction Materials Transportation Guide
The United States construction industry is massive. Industrial, commercial and residential sectors generate over $1.23 billion for the American economy, and construction continues to grow at a furious rate. With no sign of slowing down on the horizon, building products are in high demand. That requires solid and steady support to transport a variety of construction materials safely and efficiently to and from sites.
Trucking is the American construction industry’s most essential infrastructure. Trucks carry approximately 71 percent of all freight in the United States. That includes nearly all bulk construction materials such as roofing, lumber and concrete. Even furniture and household goods depend on truck transport to get finished products from factories to family rooms.
Without transportation support, the economy would slow to a halt. An estimated 3.6 million Class 8 trucks move 10.5 billion tons of freight throughout the country. Many of these trucks are owner-operated or belong to fleets. However, more and more freight movers in the construction world choose to rent their trucks and related construction equipment.
Renting construction equipment offers many financial benefits. Equipment rentals provide a versatile platform where builders can quickly respond to changing needs. Renting equipment to transport construction materials allows for precise planning, flexible options and cost-effective solutions.
Jump to a section:
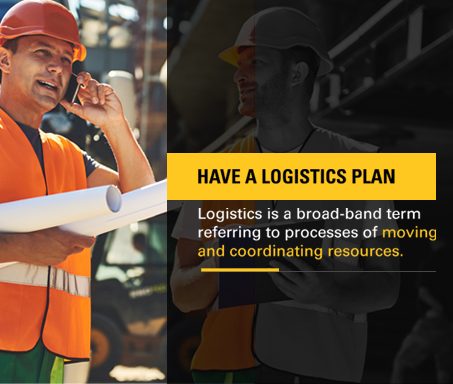
Have a Logistics Plan
Construction material logistics planning entails managing materials and equipment both to and from job sites. These two vital processes are inbound logistics and outbound logistics. Both of these equipment and material management activities require a detailed and thorough plan. A company’s logistics plans include how to efficiently purchase or rent equipment, source materials and transport them to a workplace. If building products and equipment don’t arrive on time or in the right quantities, a company can suffer.
Construction material logistics plans also require the right materials or equipment to arrive in the right amount at the right place and time. In larger construction projects such as buildings, bridges or roadways, logistical plans can be highly complex and involve thousands of intricate details being merged into a seamless flow. Regardless of how sophisticated or simple logistical plans can be, all construction material and equipment transportation coordination has these same essential elements:
- Inbound transportation logistics: Inbound transportation is highly sensitive to a reciprocal relationship between cost and time. Products and machinery have to be available exactly when needed. Delayed deliveries can stop production while early arrivals can make material and equipment management stressful.
- Outbound transportation logistics: No matter how detailed the logistics plan is, there will always be some excess material that needs returning. Rented construction equipment also has to go back to the dealer promptly to avoid unnecessary costs. Part of outbound transportation logistics also includes waste disposal following local regulations.
- Construction material logistics: Different construction materials arrive at different milestones throughout the project, requiring skilled coordination to ensure a smooth workflow. Good material logistics also account for the true costs involved in transporting materials, such as truck rental fees, operating costs and fuel expenses. Included in material logistics is also the cost associated with loading and offloading.
- Construction equipment logistics: Having a construction material logistics plan starts with knowing what machinery and attachments are required for specific tasks. Equipment logistic plans also identify timeframes when vital tools have to be sourced, transported, used and returned.
- Site management logistics: A construction manager has to prepare sites to accept deliveries as they arrive and have the resources present to efficiently deal with removing items from trucks, securely storing them and having them available precisely when needed. Any break in logistical chain links can cost thousands of dollars in lost time and productivity. Good site management plans account for every logistical step required for smooth trucking to and from construction sites.
- Communication logistics: Clear and concise communications are the key to successfully executing construction material and equipment logistic plans. Everyone involved in the supply chain needs to know what their role is and when they’re required to fulfill it. Construction software can communicate with all project team members what materials need to arrive on site and when.
- Regulation logistics: Good logistic plans account for regulatory compliance both on and off the road. Safety should be the number one concern for all construction managers who develop logistic plans. Failing to safely transport construction materials can have devastating consequences. However, tragic accidents can be prevented by knowing all transportation regulations and building strict compliance into a logistics plan.
Comply With Regulations
Trucks handle the vast majority of construction materials and equipment moved in modern America. Construction sites have specific locations that allow easy truck access where other freight movers simply can't serve the unique demands occurring at building projects.
As trucks have evolved and roads expanded, regulations have come into effect to promote order and safety. Complying with federal, state and local truck transportation rules is mandatory to address critical issues in the trucking industry.
The main truck regulatory authority in the United States is the Department of Transportation Federal Motor Carrier Safety Administration (FMCSA). This agency oversees interstate road regulations as well as certain intrastate laws. If your company is involved in construction materials transportation, it's important to understand FMCSA regulations, including the following two issues:
- Weights, capacities and truck sizes: Regulations dictate how much weight trucks can carry on the nation's road and highway networks, both for safety reasons and to protect road surfaces. Depending on the size and class of truck, the driver may require a Commercial Driver's License to comply with motor vehicle regulations.
- Hours of service: Authorities have long associated driver fatigue with trucking accidents. In response, FMCSA recently required Electronic Logging Device (ELD) units in American long-distance trucks so that drivers can track their road hours of service (HOS) and not exceed safe limits.
Transporting Construction Materials
One challenge of construction material transportation is knowing the unique requirements of specific products and how they need to be safely handled and transported. Endless categories of construction materials require safe transportation, including products like roofing materials, bulk construction materials, concrete mixtures and even furniture and household goods. The list goes on and continues to grow with the country’s economy and consumer demands.
Safe handling of construction materials requires specialized equipment, tools and techniques. There’s no one-size-fits-all solution when it comes to loading and unloading materials. Each situation requires a made-to-fit safe handling method. Here are some of the unique transportation needs to consider with these standard construction materials.
1. Roofing Materials
One of the biggest and bulkiest building products is roofing materials. Roofing materials can also be some of the heaviest construction products truckers need to move. Because roofing products come in every shape from rolled goods to palletized freight, truckers use special tie-down techniques to safely transport materials to construction sites.
Most suppliers and contractors handling roofing materials use some form of open deck vehicle. That might be a flatdeck truck set on single or tandem axles. Roofing material transportation could also be loaded on a semi-trailer attached to a separate tractor.
Vehicle selection really depends on the load size and unique characteristics of the roofing products. The key factor is what material handling equipment is available at the loading and off-loading points. For instance, many roofing material suppliers have specialized trucks with self-contained cranes and booms that extend far enough to place roofing materials on top of a building.
Other building sites have fixed construction cranes that work with on-site telehandlers to remove roofing material pallets from a truck bed and hoist them into place. Telehandlers are specialized equipment pieces designed for heavy loads like rolled membranes. For lighter products such as residential shakes and shingles, site managers might rely on trusty forklifts or skid steers equipped with pallet forks.
Safely securing roofing products on trucks and trailers is crucial. Because most decks are open, loading specialists normally use fabric straps with ratchet mechanisms. These flexible bindings conform to irregular-shaped product bundles and cinch them tightly to the deck platform. Properly secured, there’s little or no risk of roofing materials dislodging until they’re intentionally released on the job site.
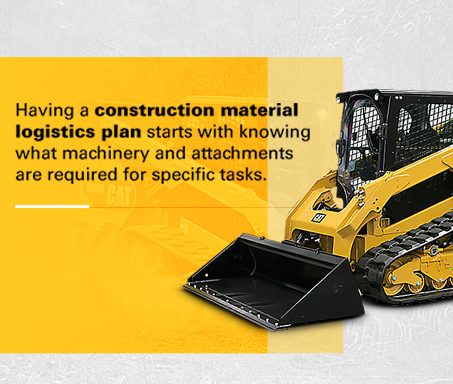
2. Bulk Construction Materials
Bulk products include a wide range of construction materials. Bulk refers to large quantity items rather than small-sized individual packages. Examples of bulk materials are aggregates for concrete mixtures, framing lumber and even building insulation.
Bulk goods present trucking challenges in containing materials and delivering them intact to their destinations. Specialized trailers like bins and tarped-in B-Train trailers are common for transporting bulk materials as well as construction equipment. There are also bulk shipping containers that work with intermodal road and rail services.
Handling bulk materials can present unique challenges for suppliers, shippers and receivers on construction sites. Packaging bulk goods can be difficult due to the inconsistent size and scope of the particular material. These are the common containment and shipping methods used in transporting bulky goods:
- Pallets made from wood, plastic, aluminum or steel
- Bins and crates constructed with lumber or mesh steel
- Roll-on and roll-off containers designed for large or loose objects
- Flat-deck trucks and trailers with hoisting capability
- Forklift or telehandler equipment at both the load and off-load zones
Bulk construction materials aren’t the only large and heavy objects routinely transported in the building industry. Many other equipment pieces are moved daily across the nation that require individual attention to ensure safe passage. Consider these construction-related machines and tools that help build America’s infrastructure:
- Aerial equipment
- Air compression equipment
- Compaction equipment
- Concrete equipment
- Crushing and screening equipment
- Earthmoving equipment
- Forest and landscaping equipment
- Material handling equipment
- Power generation
- Pump equipment
- Roadwork equipment
- Trench shoring equipment
- Trucks
- Utility equipment
- Work tool attachments
Regardless of the application, having the right construction material handling equipment can make or break a project’s success. It’s a large investment to outright purchase specialty equipment and often buying an item isn’t a practical choice. In many cases, renting tools and equipment for transporting construction materials is the wise move. Renting equipment even applies to transporting furniture and household goods.
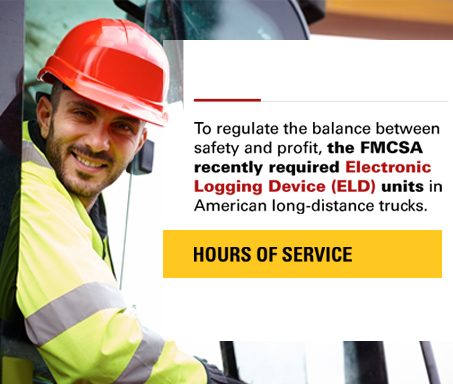
3. Furniture and Household Goods
At the end of every building project, construction managers have to think about delivering furniture and other household goods to complete the final product. Delicate items like appliances and fine artwork require special handling attention. Proper packaging is essential for protecting finished wares.
When transporting furniture and household goods, it's critical to select the right transportation equipment that's designed for this specific job. Most household movers use enclosed vans or trailer units to protect items from the weather. Exposing furniture and related goods to harsh sun or cold rain can lead to costly damage.
Packaging furniture and household goods requires a certain level of skill and planning. Professional movers use several techniques and tools to ensure there’s little or no damage done in transit. Some equipment and tactics used in the moving business include:
- Dollies and skids to prevent manually lifting heavy objects
- Special padding materials like blankets and tarps
- Tie down straps and cords designed for the moving industry
- Forklifts and powered handlers to load and unload crates and pallets
- Ramps and lifts to relieve stress and strain on workers
Transporting household goods and furniture is a specialized task. Moving companies and subcontractors are usually hired to handle fragile goods being sent to construction sites during the finishing stage. While most moving companies own their equipment outright, builders often resort to renting equipment used for handling furniture and household goods.
Renting specialized equipment makes sense. Renting saves a builder from the capital outlay required to purchase specialty equipment that they’d only use on an occasional basis. By building a good relationship with a reputable equipment dealer, construction managers ensure transport tools will be ready and available exactly when needed. Renting equipment from an established company also guarantees trouble-free service.
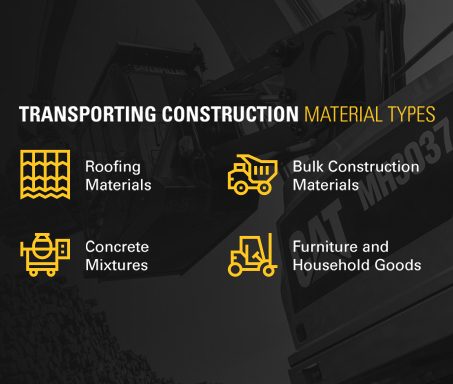
4. Mixtures
In the building industry, the term “mixtures” usually means concrete products. Concrete is a main building material in America and around the world. Without concrete, construction would be paralyzed. No known material can effectively and economically replace this vital substance.
Wet concrete mixtures are critically time-sensitive. Once ingredients like aggregates, cement powder and water connect, a chemical reaction starts the clock. Concrete mixtures are volatile and valuable. They have to be placed within certain time parameters, or they’re wasted.
Transporting and placing concrete mixtures requires specialized equipment. Most concrete available on the American market is pre-mixed at a concrete plant and delivered to the construction site in a semi-liquid state. In the concrete business, this process is called “Ready-Mix."
Planning for the transport of concrete mixes requires forethought and precise communication. They also need competent truck drivers and the right mixing equipment. Here is a list of typical concrete mixing, placing and handling equipment used in the Ready-Mix business:
- Cement-mixing trucks with rotating bins to keep mixes from early curing
- Concrete pumper trucks to transport wet mixes from the truck to the forms
- Vibrators to settle wet concrete mixes within their curing forms
- Power trowels for smooth finishing concrete flatwork
- Concrete core drills, power tools and jackhammers for additional work
Mixing equipment and the wide variety of concrete work tools are expensive and specialized. Many construction managers and logistics planners find renting these necessary items is much more economical than owning them. Construction managers can get the flexibility and cost-effectiveness they desire by renting equipment from a reputable source like The Cat® Rental Store.
Renting Construction Material Transportation Equipment From Caterpillar
Construction managers experienced with logistics planning often see the benefits of renting their equipment. To keep overhead costs low on an already tight construction project budget, renting can be more practical and more economical as well. Renting equipment has many advantages, including having the right equipment available for the right job at the right time.
The Cat Rental Store network offers the world’s largest rental fleet of construction equipment. From earth-moving machinery that Cat is famous for to power generators that can save a job from disastrous power outages, The Cat Rental Store has an enormous equipment selection. Our inventory includes the widest selection of Cat equipment as well as over 70 other allied equipment brand names that help builders and logistic managers get the work done.
Transporting equipment from a Cat Rental Store location is just a phone call away. Whether the project is new building construction, roadworks, utility contracting, industrial complexes or landscaping projects, your local Cat Rental Store has the exact machinery necessary to arrive on time, service the site and be picked up and trucked back when the job is done.
Cat Rental Stores also have the expertise to help you choose from a wide range of construction equipment and material handling machinery. Get the job done smarter and faster with The Cat Rental Store. Call 1-800-RENT-CAT or browse our equipment online and rent whatever you need from people who do whatever it takes.
Find The Cat Rental Store Near You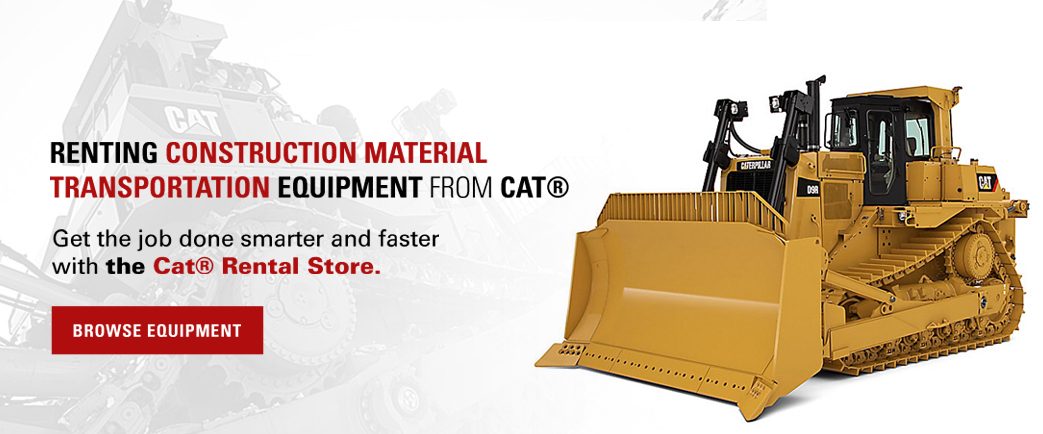
Related Posts
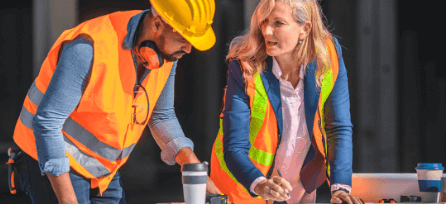
Construction Project Management: The Ultimate Guide
There are a lot of moving parts within a construction project, and construction project management helps pull everything together. Learn more today.
Read More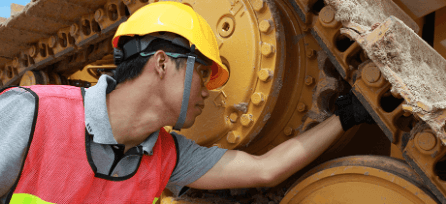
What Causes Construction Project Delays?
Construction project delays impact productivity and reduce profit margins. Discover the top reasons for construction project delays and learn how to avoid them.
Read More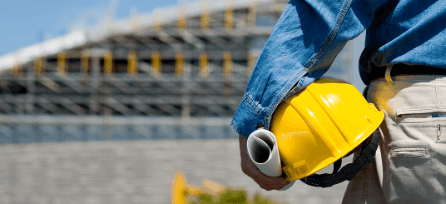
Construction Risk Management
Risks are an inevitable part of life, but you can take an active role in responding to risks through risk management. Learn more with The Cat Rental Store.
Read More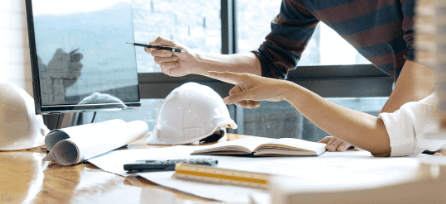
The Construction Software Guide
If you're looking to optimize your construction company's operations, construction software can be a great tool to utilize. Learn more with our guide.
Read More