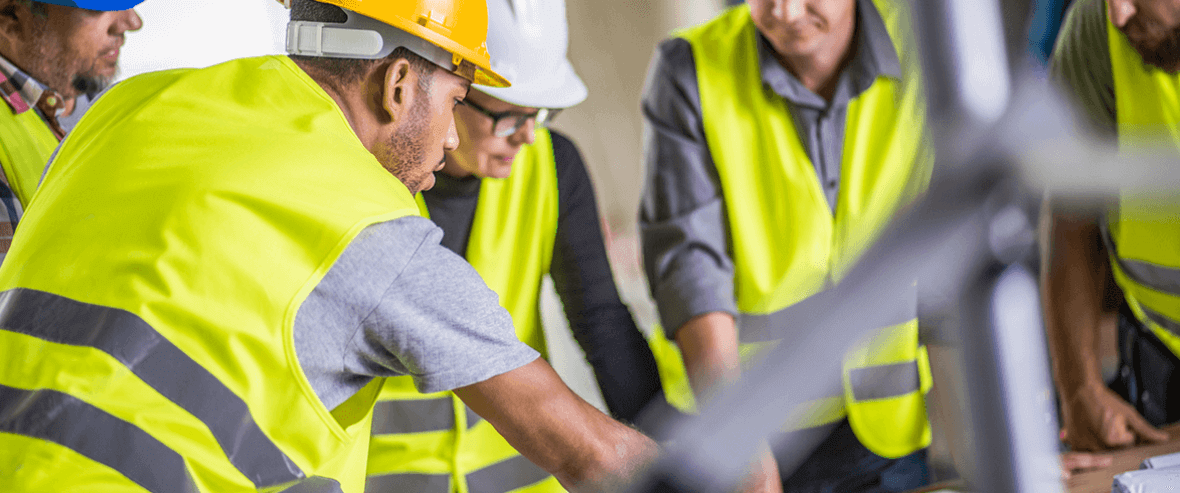
Lean Construction: The Ultimate Guide
Efficiency can often be elusive in the construction industry, where over 90% of world infrastructure projects come in over budget or late. One approach that was developed to manage this lack of productivity was the idea of Lean construction.
Lean construction looks for continuous improvement across all dimensions, but maximizing efficiency and reducing waste are common denominators. This method of project management offers exceptional results to those who practice it and can help increase client satisfaction, worker safety, profit margins and much more.
Jump to a section:
What Is Lean Construction?
Lean construction aims to improve projects across all aspects. It doesn't choose cost over efficiency or quality over both — instead, it works to maximize efficiency and minimize waste wherever possible. Many factors contribute to productivity, and businesses can often eliminate several different types of waste in construction.
One of the overarching elements of Lean construction is communication. Nearly every part of the approach requires exceptional communication, so everyone knows how the project is progressing and where they can make adjustments. A successful Lean project involves strong relationships between the different parties. This factor is especially important in construction due to its unpredictability. Designers, contractors, stakeholders and anyone else involved should be able to make informed decisions based on everyone else's schedules to support the overall success of the project, not just their task.
One reason some people resist Lean construction is because they see it as a carryover from a different industry and feel that it doesn't apply to construction. While it's true that Lean Design initially came from manufacturing, its basic principles apply readily to construction, which has plenty of evidence to back up the benefits.
McGraw Hill Construction found 84% of firms that adopt Lean construction experience higher-quality projects, while 80% of firms find it provides greater customer satisfaction. Other benefits include improvements in safety, completion times, productivity, risk management and profitability.
Lean construction is an approach that can vary widely between projects and firms, so there is no set of rules to define it. Instead, we have some guiding Lean construction principles to help determine and direct Lean practices.
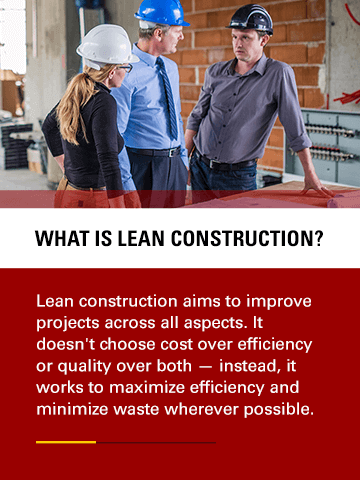
Principles of Lean Construction
Lean construction principles like concurrent design and engineering and techniques to eliminate bottlenecks can help bring the approach of maximizing efficiency and reducing waste to life. They apply to the project as a whole, and for the most part, the overall project is more important than any one task. The following are some of the principles of Lean construction:
1. Value
One major tenet of Lean construction that guides many other decisions is the definition of value. In a traditional approach, a contractor simply meets the specifications provided to them. But from client to client, expectations can differ. Some would prefer a project that gets done on-schedule to one that costs more, while another might want higher-quality materials, even if it means going over budget.
The job of someone pursuing Lean construction is to identify these client needs and use them to direct decisions throughout the project. They might conduct plenty of research or inquiry to fully understand what the customer wants.
Once they define the client's values, Lean construction involves laying out the value stream. This step is one that identifies a schedule and what resources are necessary to meet the client's needs, such as labor, materials, equipment and education or training. If a Lean construction worker identifies resources that are unnecessary or don't add value to the overall project, they can eliminate them to save time and money.
There are many different types of wastes within construction that form the acronym DOWNTIME. In Lean construction, workers try to eliminate as many as possible:
- Defects: Defects occur when production has to be scrapped or redone due to inaccurate work. Reducing errors and improving communication can help ensure the job gets done right the first time or that any adverse effects are less influential to the rest of the project.
- Overproduction: Overproduction involves creating something before people need it. While working ahead can seem smart, it can also become affected by changes that occur in other phases of development. This leads to rework, which is a costly duplication of efforts.
- Waiting: Waiting refers to the time spent standing around for a previous step to be completed before you can move on with the next. Waiting also occurs when materials aren't available as workers need them. These events may not always be avoidable, but appropriate planning and a sure knowledge of deadlines can help minimize them.
- Non-utilized resources: This form of waste often occurs when workers and their tasks are mismatched or when available resources aren't used to their fullest extent. Involving and seeking input from the source of the work can help you gain a better understanding of resources for appropriate use.
- Transportation: Any unnecessary movement is a waste of resources. It may take up time, fuel and money. This concept applies to moving people, equipment, supplies and even information. Administrative tasks, such as having a meeting on data only relevant to a few people, still take time and money to complete.
- Inventory: In construction, inventory can refer to information or materials. Materials acquired before they are needed may sit around in storage and create unused inventory that may need transportation or become damaged. As for information, decisions that are made too far in advance can easily get altered down the road. By the time they are needed, the situation can change, necessitating more work to research and inform others of the new decision.
- Motion: Excessive motion can refer to the complication of processes and unnecessary distance between people and items. Workers who are too far away from their tools and materials will spend more time getting to them. If a contractor requesting information has to go through several different channels to get their answer, it wastes time.
- Excess processing: Overprocessing involves doing more work than is needed to meet the client's needs. It may come from a misinterpretation of the client's desires, a disregard for them or poor planning. Avoiding overprocessing involves paying close attention to the previously defined values. Ensure that each action taken adds value to the final product for the client.
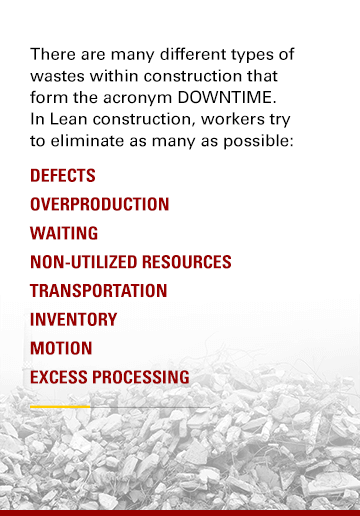
2. Flow
You may have noticed that many of the principles above rely on exceptional scheduling processes. That's because a smooth workflow is vital. With a quick-moving project, you can remove bottlenecks and other issues that can impede work.
Part of creating even flow is leveling the workload, which refers to creating consistent outputs that enable a steadily moving schedule. Erratic workflows make it difficult to depend on tasks that need sequential completion. Leveling the workload helps make things predictable and reliable. Communication is a key player in establishing a consistent workflow. Different parties must communicate with each other if they fall behind or run ahead of schedule so that others can adjust accordingly.
3. Pull
Pull refers to the idea of only delivering equipment and supplies as they become necessary. You shouldn't waste resources on storage and movement until workers can use them.
Using a pull-based strategy is based on downstream demand and may require backward planning to identify timelines. Often, those performing the work will assist heavily with the plan, since they know the most about their needs.
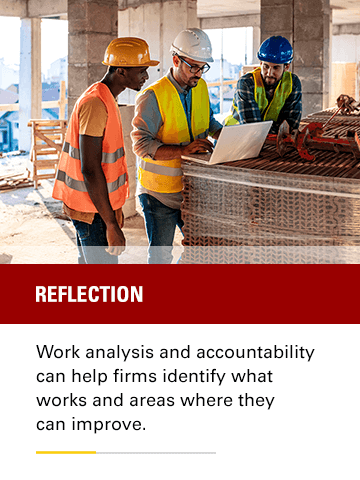
4. Reflection
Lean construction requires regular reflection on progress to foster continuous improvement. It should be an inherent part of your approach and company culture. Work analysis and accountability can help firms identify what works and areas where they can improve.
When they do so, they create a wealth of benefits for their client and generate value across dimensions. Lean construction respects the insights of each individual and sees them as a form of value that contributes to the success of the whole project.
Benefits of Lean Construction
Aside from maximizing efficiency and reducing waste, Lean construction comes with many other advantages, including the following:
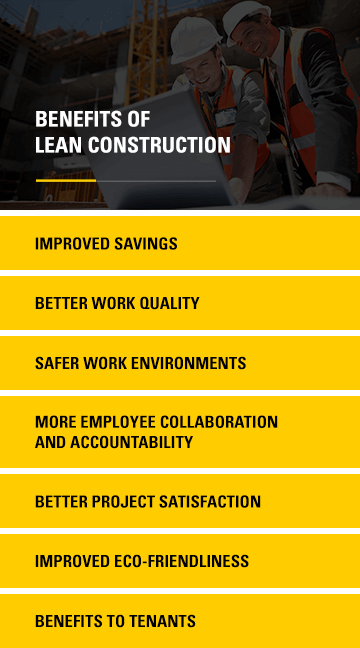
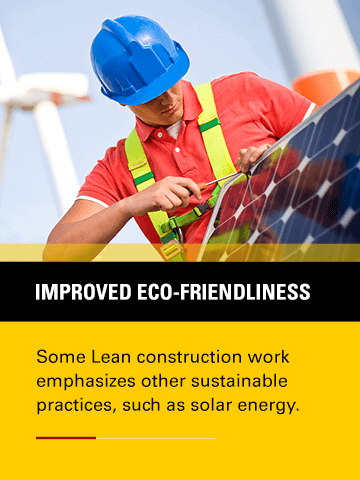
Lean Construction Strategies and Tools
Since Lean construction can take many different forms, it should come as no surprise that there are lots of strategies and tools that help make Lean construction successful. Typical requirements for these strategies include strong communication, leadership, teamwork and training.
1. Integrated Project Delivery
Integrated Project Delivery (IPD) takes a team-based approach to results. Risks are shared, design is collaborative and key stakeholders are assembled early on in the process. Teams clearly define goals with "integration" as the keyword facilitating cooperation.
Another component of IPD includes the use of modern technological programs that enable collaboration. If you've ever had to trade off paper documents for a project, you know how uncollaborative this can be. Each person works on their part and sends it to the next person. There is no co-creation or sharing of ideas to support new discoveries. IPD uses digital projects and virtual meetings where necessary to support this goal of collaborative work.
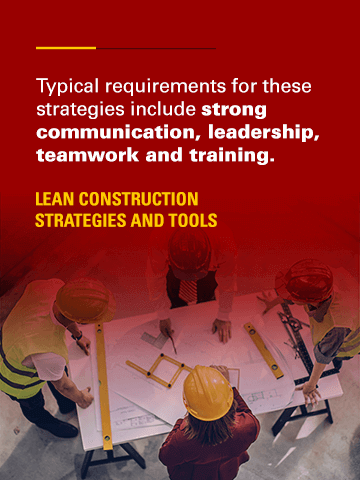
2. Last Planner System
The Last Planner System is a scheduling method that supports Lean construction's goals of smooth workflows, improved efficiency and collaboration. It includes a master plan where different partners set up plans for different phases, considering their future needs and goals. There are five processes identified within the Last Planner System, and tasks will overlap with each other as they move through the different phases:
- Collaborative programming: In this phase, stakeholders create and agree on a specific production sequence.
- Make ready: The goal in the make ready phase is to prepare tasks to be free of constraints and, as the name implies, get ready for work.
- Production planning: Also called weekly planning, this phase involves regular meetings to identify tasks for short-term periods, such as the next few days or weeks.
- Production management: A task in production management is one that gets monitored to ensure everything goes according to plan.
- Measurement, learning and continual improvement: In the last phase, review and education from recent tasks are critical to inform work moving forward and learn from issues or successes.
One of the strengths of the Last Planner System is that it's great for identifying possible problems that will influence other tasks, so stakeholders can make adjustments. If constraints appear, the various parties can respond and avoid bottlenecks.
While the master plan is a great guideline, the Last Planner System acknowledges that plans are forecasts, which become more wrong as they expand over time. A plan made for two months from now can't be as detailed or as accurate as a plan for two days from now, and the Last Planner System accounts for that.
Finally, transparency is another significant part of this schedule. Some teams will make this schedule available on-site and solicit feedback to make sure each step is as informed as possible.
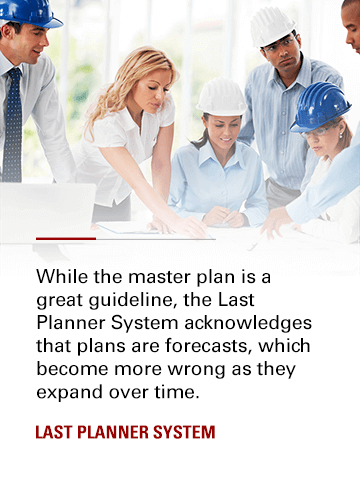
3. 5S Process
The five S's of Lean construction are as follows:
- Sort: Sorting tools allows you to remove unnecessary items and set aside rarely used ones.
- Set in order: An organized workspace provides easy access to tools and equipment. For smaller tools, use vertical wall storage, bins and toolboxes. Larger equipment, like vehicles, should have designated spots, such as within markings made from floor tape.
- Shine: Give everything a good scrub to help maintain it and foster a more pleasant work environment.
- Standardize: Maintain similar organizational systems across locations. Any crew or team member should be able to know their way around different service trucks or toolkits. Plus, it's easier for new team members to hop in and spend less time learning where everything is.
- Sustain: Routines help solidify this behavior and ensure it stays in place. Inspections and input from team members can also help create routines.
Many like the 5S process because these factors result in immediate changes to the workplace. They're also simple to enact and can be done in almost any area or type of worksite.
4. Total Productive Maintenance
Total Productive Maintenance (TPM) looks to eliminate setbacks that come from machinery issues such as breakdowns and accidents. It focuses on proactive maintenance procedures and actions that can maximize the equipment's efficiency.
TPM may involve precise maintenance schedules for routine work or tasks required after a specific number of use hours. It includes inspections, thorough training and education. In addition to machine care, safe operation is also a component.
5. Single-Minute Exchange of Dies
If you've ever watched a pit stop in car races, you've seen some Single-Minute Exchange of Dies (SMED) in action. SMED is all about minimizing non-productive time during changeovers. If you can reduce the time it takes to tear down or set up the equipment needed for a task, you can minimize the time spent doing anything other than the task itself.
Employing SMED practices typically involves a thorough analysis of current procedures and the duration of each step. You can further split these steps into internal and external activities. Internal activities are only possible while a process is stopped, like removing the tires on the race car. In contrast, external activities can occur alongside the process, such as getting the tires in place where the car will be.
If you can turn some of those internal activities into external ones, you may be able to reduce the time where the process is stopped. Of course, other methods of streamlining will also help make the process faster.
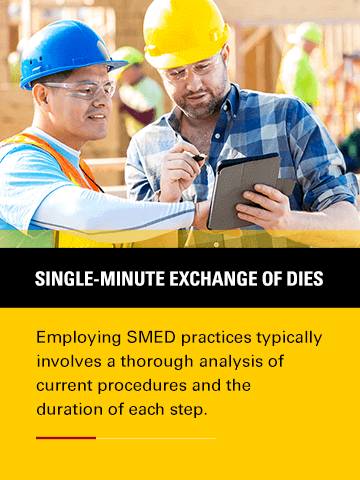
6. Kaizen Events
Kaizen events are short-term workshops, typically occurring within a week, aimed at training in specific areas for improvement. They may focus on reducing travel distances, increasing output and analyzing a value stream, among other goals like 5S and TPM.
These events have clear scopes and goals and help to get your team on the same page regarding Lean construction and its practices.
7. Cloud-Based Tools
The cloud is gaining popularity in many industries, construction included. It is an excellent resource because of its flexibility. Users can access documents and resources from any device with an internet connection. It's also an excellent tool for collaboration, as different contributing partners can hop on at the same time and work on projects simultaneously. Plus, changes occur in real-time, so everything is as up-to-date as possible.
Many project-management cloud tools exist for tasks such as:
- File-sharing
- Scheduling
- Document management
- Accounting
Many programs are specific to construction management and can offer plenty of relevant capabilities within one piece of software.
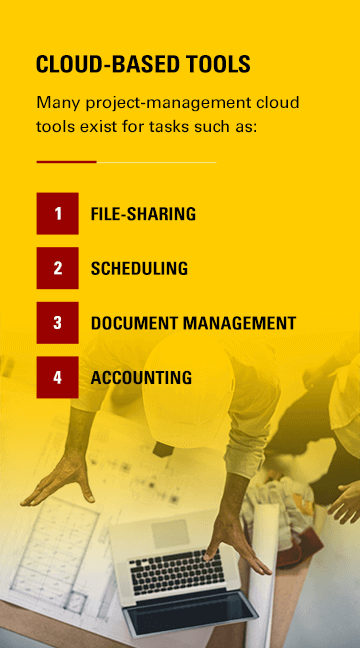
Partnering With The Cat® Rental Store for Lean Construction Jobs
Lean construction is all about minimizing waste and maximizing your investments. When making any decisions, it's critical to have all the options in front of you. One valuable choice you may make is to rent any new equipment you need.
Renting can often be a more cost-effective and waste-reducing selection. You won't have to use resources on maintenance, and you won't need to invest in a vehicle you may not need in the long run. It also increases flexibility, allowing you to respond to changes quickly and only access the equipment when you need it.
Take a look at our selection today or contact your nearest dealer to learn more about renting from The Cat® Rental Store. Rent what you need from those who know what it takes.
Find The Cat Rental Store Near You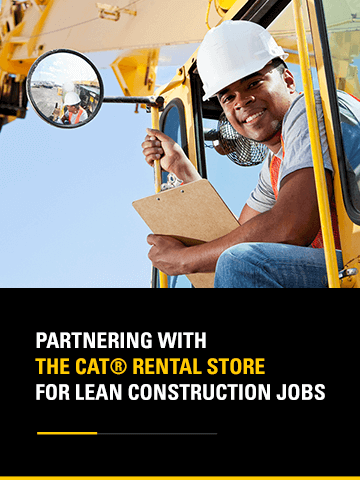