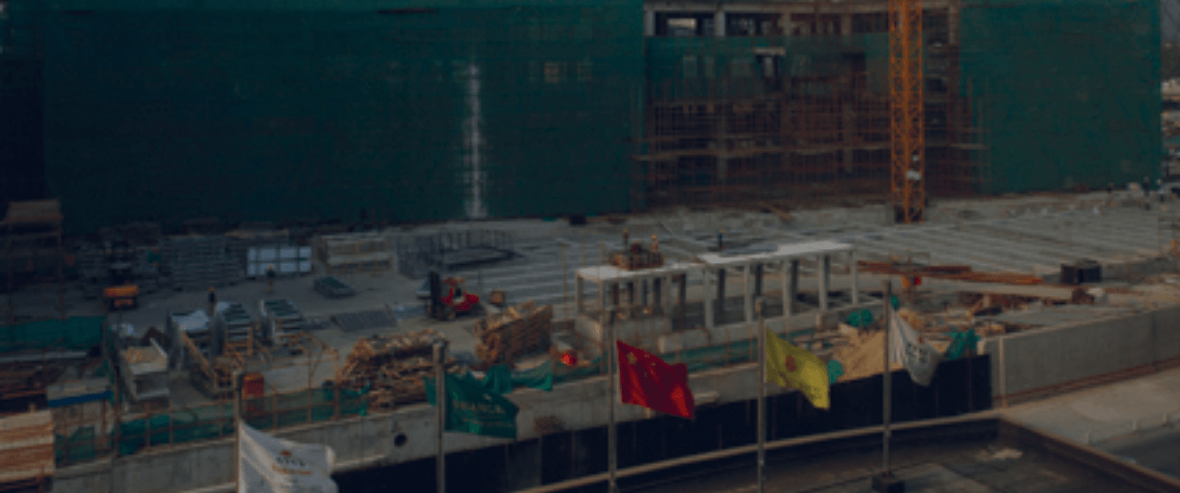
What Is Modular Construction?
What Is Modular Construction?
Modular construction is an innovative process with many benefits. With this type of construction, buildings are created as individual sections or "modules," which are constructed off-site in a controlled manufacturing facility. These modules are then transported to and assembled at the final building site. They use the same materials and meet the same codes and standards as conventionally built facilities, but typically take about half the time.
MODULAR CONSTRUCTION VS. TRADITIONAL CONSTRUCTION
There are several key differences between modular construction and the traditional variety. One of the main differences is that the majority of modular construction takes place within a manufacturing facility, while traditional construction occurs on the final building site and happens from the ground up.
The traditional approach to construction requires you to get the site ready before you can start the building process. With modular construction, however, site preparation can begin while the manufacturing facility is producing the modules, which means this type of project can take significantly less time to complete.
How Is Modular Construction Different Than Traditional Construction?
Aside from construction location and site preparation, there are many additional distinctions that make modular construction so much different than the traditional variety. Through understanding these deviations, you'll understand why companies are beginning to switch from traditional to modular construction methods.
Project Schedule
Perhaps the most significant difference between modular and traditional construction is the way each method executes its building processes. Though both styles involve most of the same steps, the execution will vary based on their capabilities.
Modular and traditional construction differs in the following operations:
- Design and engineering: Modular construction offers more opportunities for interior and exterior building customization than traditional construction. The traditional engineering process often involves an architect the company hires to create a plan or a builder who will base the building design on a former project.
- Site development and foundations: While both processes involve groundbreaking, excavation and foundation building operations, the modular method begins building construction while these are ongoing.
- Building construction: Through modular construction, workers assemble the building on a factory assembly line inside the manufacturing facility, where elements like inclement weather and vandalism cannot impact the process. Traditional construction occurs on-site, meaning processes are dependent on weather conditions and require precise scheduling.
- Modular installation: This step is exclusive to modular construction. At this point in the process, the building is nearly finished and only requires workers to wait for module delivery and fit the pieces together.
- Site restoration: Both site restoration processes involve repairing any asphalt, concrete or landscaping that was disrupted during construction. However, this procedure occurs much earlier in the modular construction schedule than it does in traditional construction — by the time restoration begins in traditional construction, the building is already finished and ready for occupancy through modular assembly.
Time
Because traditional construction processes are carried out in a linear fashion, workers must wait to execute the next step until the previous one is complete. The lag time in between increases how long it takes to finish the project, which could take anywhere from six months to a year.
On the other hand, modular construction enables builders to start the foundation and manufacture the building simultaneously, significantly shortening the process. Through the modular method, you can complete a building in as little as two to four months.
Cost
Modular construction tends to be more cost-effective than traditional building methods because of how much less time the process takes to complete, resulting in increased return on investment (ROI) due to earlier occupancy. The modular approach also helps companies cut down on construction expenses through its lower cost of assembly and installation.
Because traditional construction takes much longer to complete and is highly dependent on weather conditions and laborer abilities, the associated costs are much higher.
Quality Control
Because the entirety of the modular building process takes place in a manufacturing facility, it allows for greater quality control during fabrication than traditional construction. Factories provide a controlled environment with constant supervision from higher-ups, ensuring that all modules are manufactured according to industry regulations.
Traditional construction takes place on-site in a less controlled environment, making it more challenging to maintain quality standards.
TYPES OF MODULAR CONSTRUCTION
There are two main types of modular construction:
- Permanent Modular Construction (PMC): With PMC, buildings are made in deliverable module sections for permanent placement on a site. PMC is often used for homes as well as commercial facilities, and it represents an efficient and sustainable alternative to traditional construction.
- Relocatable buildings: Relocatable buildings are designed to be repurposed or reused multiple times and transported to different building sites. They are ideal for temporary space needs for schools, offices, clinics and sales centers. With fast delivery and low-cost reconfiguration, they offer great flexibility and are a highly sustainable option for temporary space needs.
BENEFITS OF MODULAR CONSTRUCTION
In addition to significant time savings, there are many other advantages to modular construction methods:
- Less material waste: Building in a factory enables you to more easily recycle, protect materials and control inventory to help eliminate waste.
- Greater reuse: Modular buildings can be disassembled and reconfigured for new use, which reduces the demand for materials and minimizes the amount of energy needed to create the building.
- Fewer weather issues: With as much as 90% of modular construction occurring inside a factory, the risk of weather damage or delay is significantly reduced.
- High quality: Modular homes are built to the same codes and standards as traditionally constructed homes, and they use the same high-quality materials.
- Safer construction: Indoor construction environments help to reduce the risk of accidents for workers.
- Unlimited design options: Modular buildings can be highly customized and built to match any aesthetic.
CONTACT THE CAT® RENTAL STORE FOR YOUR CONSTRUCTION EQUIPMENT NEEDS
To save even more time on your modular construction project, trust the exceptional rental equipment available from The Cat® Rental Store. We supply a wide range of earthmoving, material handling and other types of construction equipment at affordable rates and flexible rental periods.
Browse our inventory online to find the equipment you're looking for. You can also call us at 1-800-RENT-CAT for assistance, more information or to get a rental quote on anything in our extensive inventory.
Find The Cat Rental Store Near You