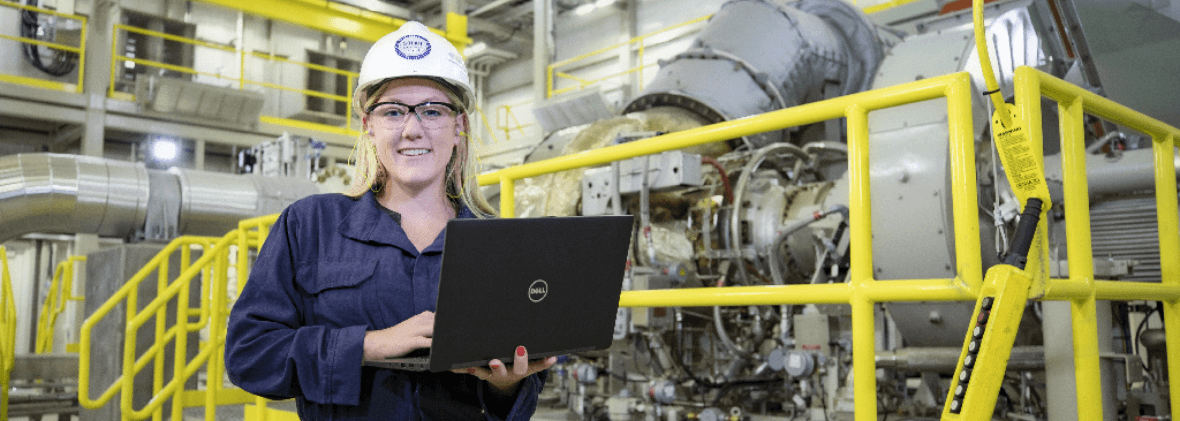
7 Ways to Cut Your Project Costs Without Cutting Quality
Construction professionals always aim to complete jobs on time and according to budget. It can sometimes be a challenge to finish an assignment by a given deadline, but it is essential for your team to follow a course of action without cutting corners. Fortunately, analyzing your current process for starting an assignment may point out some changes you can make to save money.
Here are some tips on how you can cut project costs without cutting quality:
1. Hire the Best Workers
The quality of your workforce can make the difference between a job that goes smoothly or one that's riddled with issues and falls behind schedule. One of the most effective ways to reduce construction project costs is to vet prospective crew members thoroughly during the hiring process.
Conduct comprehensive background checks and contact previous employers to learn more about the quality of the candidates' work and other crucial areas such as attendance and the ability to function as part of a team. You also verify they've fulfilled the necessary licensing requirements if applicable.
You may need to pay higher wages to the most qualified workers and incur additional hiring costs. However, better craftsmanship, increased productivity and reduced project completion times should more than offset these expenses.
2. Prioritize Employee Training
Thorough training sessions are crucial for maintaining safety and efficiency. Decision-makers often forget that teams can only utilize the resources available to them if they know how to use them properly. Allowing an individual to operate machinery without training is dangerous and could result in expensive damage or fines.
Depending on the task and equipment, employee training programs take anywhere from a few hours to less than a week to complete. Staying up to date with employee qualifications puts you in a position where you can confidently delegate tasks and create an environment where few human errors occur.
Enrolling workers in training courses is critical for ensuring job site safety, as well as an excellent way to limit costly mistakes that lead to fleet repairs and material waste.
3. Provide High-Quality Tools
Even the most qualified and experienced workers need the right equipment for optimal performance. Once you've hired and trained your crews and they're ready to go to work, make sure they have the best tools for the job. Choose quality products that can withstand the rigors of heavy use under demanding conditions. Have your crew managers verify that each individual is using the appropriate tool for a specific application.
Also, implement stringent security measures to protect the tools when they're not in use. Secure an on-site area where you can lock up the equipment at the end of the day. Don't let workers take home any items that don't belong to them.
4. Buy Building Materials in Bulk
Project managers are in charge of ordering the supplies crews will use to build a structure. If you know that your business frequently uses wooden sheets, nails, hardware, concrete or specific aggregates, compare prices from wholesalers and consider buying in bulk. Having an excess supply of materials you frequently need helps to speed up construction and cut costs. This practice also allows you to stay clear of repeat shipping fees.
Buying raw materials from a wholesale dealer will give you the lowest cost per unit. Before purchasing in bulk, ensure that you have a safe place to store your goods so they stay in pristine condition.
5. Improve Job Site Practices
Take a closer look at your on-site processes and procedures. You might be surprised at how much time, labor, materials and resources you can reduce — and how much money it can save you.
Implementing sound site management practices begins with hiring competent project managers who will supervise your workers closely and monitor their activities. These professionals should possess exceptional communication skills and have the ability to set goals for every crew member and ensure they meet them.
Another way to reduce your job site expenses is by adopting lean construction procedures. These methodologies can optimize your processes by significantly reducing waste.
6. Utilize Technology
Taking advantage of the evolving construction technologies is another excellent way to reduce construction project costs. Consider investing in innovations such as drones that provide overhead site images to assist with planning and monitor the work's progress. There are robots that can increase site surveying accuracy and perform other automated tasks to minimize costly human errors.
7. Rent Appropriate Equipment for the Job
Professionals searching for ways to save money on a construction project must think about their current fleet. Is your team equipped to tackle the task at hand? Renting machines from a reputable source like The Cat® Rental Store allows you to plan for new opportunities without the commitment of a long-term investment.
Not all businesses wish to own their equipment. Whether you're in digging or demolition, renting gives you the flexibility to acquire machines based on an agreement that works for you. The Cat Rental Store has over 1,300 locations around the world. By partnering with your local dealer, your construction business can benefit from:
- Machines regularly serviced by expert technicians.
- Delivery of orders directly to your site.
- Rental agreements on a short- or long-term basis.
- Access to the latest technology for your industry.
Browse The Cat® Rental Store for Industry-Leading Equipment Rentals
The Cat Rental Store introduces you to rental machines from over 70 different brands. All of our offerings are organized by category so you can find rental machines suitable for your applications. Locate a dealer in your area to see the equipment in person.
Call the experts at 1-800-RENT-CAT for details about our products. You can also complete a form online to receive a quote on the machine you need.
Find The Cat Rental Store Near You