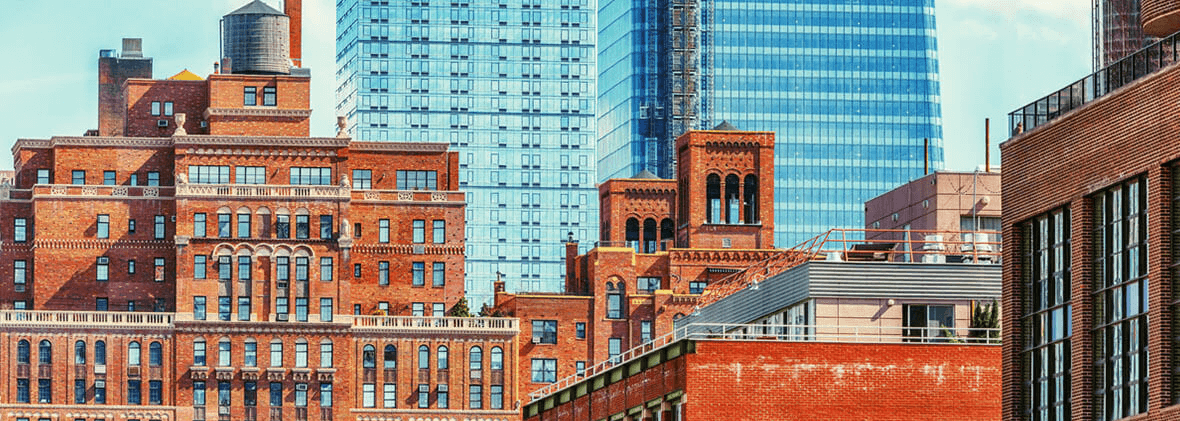
The 5 Building Construction Types
Many buildings look similar at first glance, but the underlying materials play a significant role in the building's durability and cost, especially in times of emergency. Whether you're the project manager for a new office building or a contractor looking to build a tiny home, it is imperative to understand the building's material needs to ensure the structure is safe, durable and reliable.
Building codes define structures between five building construction types to reveal crucial information about the building. In this guide, you can discover the various construction types and why this knowledge is essential for the construction industry. Discover the building construction types and the pros and cons of each one now.
Jump to a section:

Construction types are vital for everyone in the construction industry and essential responders, such as firefighters. Different construction techniques and materials will affect a building's resilience to hurricanes, fire and earthquakes, so construction workers must understand the impact of their choices. Their work will contribute to the building's future safety, making it essential to understand the pros and cons of each building type.
Additionally, responders can use construction types to develop an effective plan for tackling various problems. For instance, firefighters can use construction types to gather an understanding of how a fire will spread through different buildings. This knowledge allows these responders to make decisions about water and ventilation to minimize dangers and save lives. Furthermore, these responders can use building types to anticipate hazardous situations such as collapse, flashover and back draft.
Understanding the Construction Types
Every building falls into one of five categories. This classification establishes a building's fire resistance, allowing construction workers and responders to know how a structure will fare during an emergency.
The five building construction types incude fire-resistive, non-combustible, ordinary, heavy timber and wood-framed. The most fire-resistant buildings will fall into the Type l category, while lightweight structures with combustible materials will appear in the last category. Keep reading to learn more about each type and the pros and cons of each.
1. Type l — Fire-Resistive
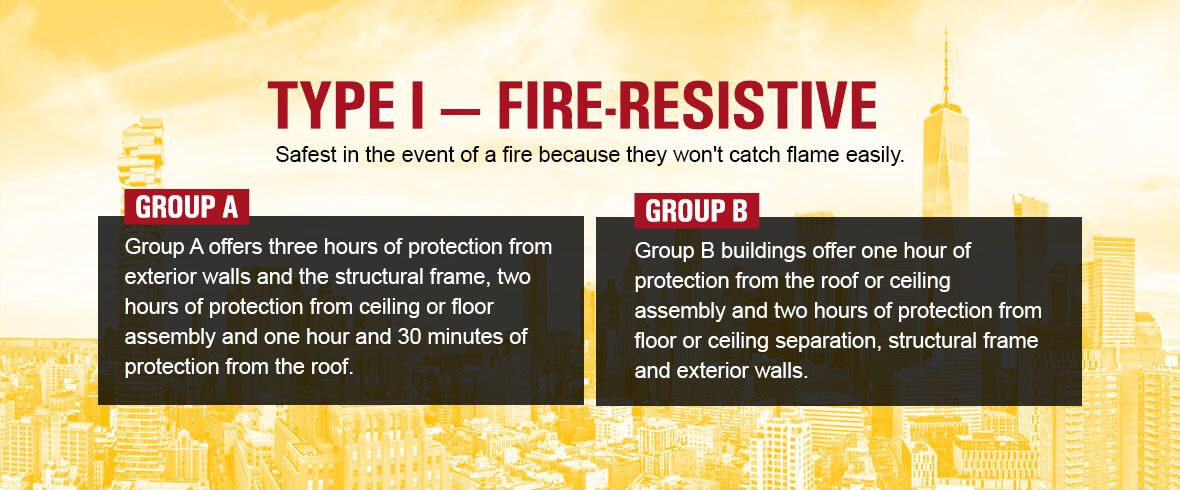
Buildings within this category are often more than 75 feet tall. These structures typically function as commercial spaces or high-rise housing units. New York skyscrapers are an example of this type, and a significant amount of concrete and steel beams will likely feature in these buildings.
The materials and design of this type allow these structures to be the safest in the event of a fire because they won't catch flame easily. Additionally, these buildings can withstand high temperatures for prolonged periods. All building elements must be non-combustible in this class, including interior and exterior walls, structural frames, interior and exterior partitions and roof and floor construction. You'll often find protected steel and reinforced concrete covered in resistant coatings in these structures, making them more suitable for large use cases than single-family homes.
Type l buildings can withstand fire for about two to four hours and are unlikely to collapse during a fire. However, you can also further classify establishments in this class as Group A or Group B:
- Group A: Group A offers three hours of protection from exterior walls and the structural frame, two hours of protection from ceiling or floor assembly and one hour and 30 minutes of protection from the roof.
- Group B: Group B buildings offer one hour of protection from the roof or ceiling assembly and two hours of protection from floor or ceiling separation, structural frame and exterior walls.
Some Type l buildings have specialized systems to mitigate fire spread, like self-pressurizing stairwells, smoke doors on elevators and self-closing fire doors. The structure materials in these buildings are fire-resistant and non-combustible. Additionally, firefighters can often reach fires more easily due to the construction components, allowing them to quickly extinguish the fire and guide people to safety. Firefighters secure the stairwells during a fire to ensure safe passage for building occupants to escape.
It is worth noting that these buildings are often the most costly to build, although they offer the most protection. Additionally, exposed steel can experience wear after long periods, and windows and roofs can prevent ventilation during fires.
Examples of Type l buildings could include:
- Assisted living facilities
- Hotels
- Group homes
- Care facilities
- Halfway houses
- Apartment homes
- Dormitories
2. Type ll — Non-Combustible
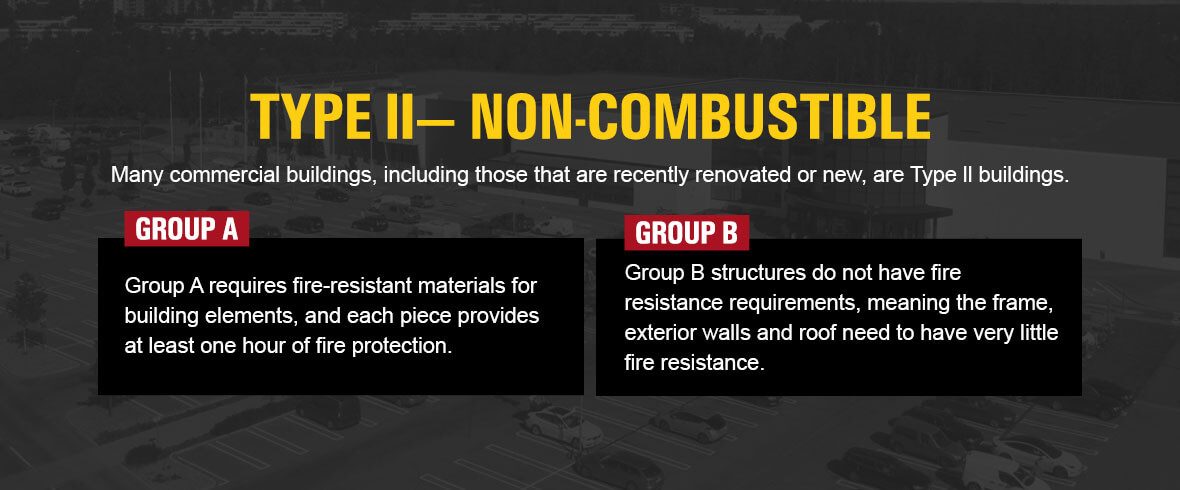
Many commercial buildings, including those that are recently renovated or new, are Type ll buildings. These buildings are prone to collapsing if flames expose the roofs to high temperatures, but these structures often feature fire suppression systems.
These buildings often feature materials like reinforced masonry and tilt-slab construction. These materials are fire-resistant, and the structures typically have non-combustible, lightweight concrete in the roods. Similar to Type l structure, Type ll buildings require non-combustible materials like concrete and stone to comprise the exterior, roofing, framing, walls and floors, but there may be flammable materials, like rubber and foam, present in the construction. Depending on the exact materials, this class can provide one or two hours of burn resistance.
There are also two groups for this building type:
- Group A: Group A requires fire-resistant materials for building elements, and each piece provides at least one hour of fire protection. People often use Group A buildings for smaller structures that cost less to build to preserve their life spans.
- Group B: Group B structures do not have fire resistance requirements, meaning the frame, exterior walls and roof need to have very little fire resistance.
Firefighters will attempt to ventilate buildings of this type during a fire. The goal is to prevent flashovers, sudden spikes in temperature. Firefighters can use roll-up doors on the structure's exterior to increase ventilation during a fire. Without proper ventilation, temperatures can rise very quickly in these buildings, potentially leading to a collapse.
The most significant drawback of this type is the possibility of collapse. The metal roofs of these buildings are prone to collapse, even if they don't have direct contact with flames. If you do not cool the ceiling quickly, the heat can weaken steel members lacking protection, allowing them to relax, distort or expand, which can cause a collapse.
Additionally, these structures typically feature a flat roof with insulation, felt or roofing tar, which are combustible materials. In the event that a fire reaches the roof, the entire system will fail. Furthermore, the construction of these buildings can make it challenging to breach in emergencies, allow ceilings and walls to retain heat and create opportunities for steel to weaken due to corrosion, rust or fire.
Examples of Type ll buildings could include:
- Shopping malls
- New schools
- Big-box stores
- Renovated commercial structures
- Markets
- Wholesale stores
- Daycare facilities
- College institutions
- Religious buildings
3. Type lll — Ordinary
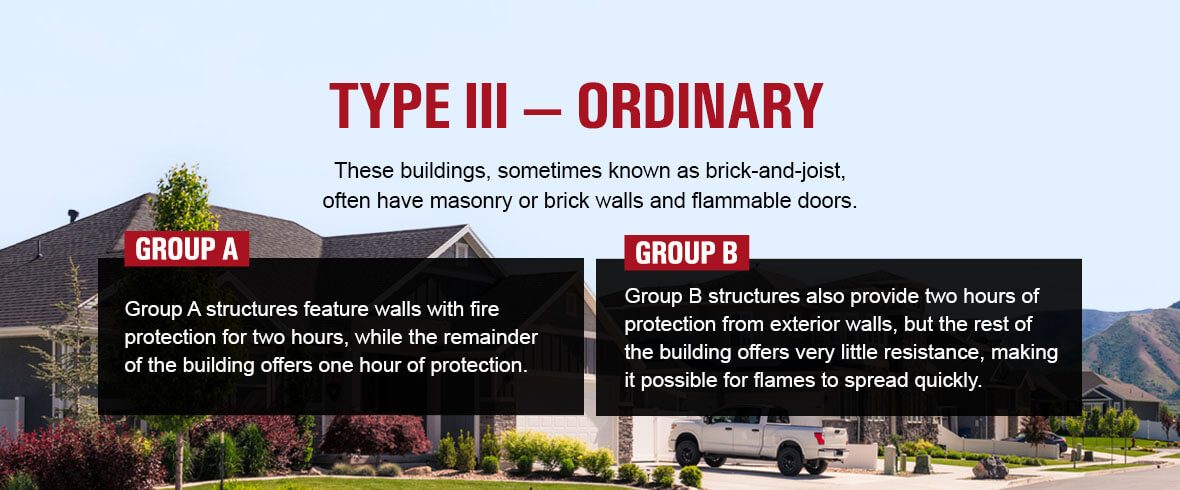
Type lll buildings have non-combustible walls and wood roofs. Older structures may have framed roofs, but newer facilities offer lightweight systems. These buildings, sometimes known as brick-and-joist, often have masonry or brick walls and flammable doors. Exterior walls could consist of precast panels, concrete block, brick, masonry or another non-combustible material. Many interior elements of these buildings are flammable. These elements include ceilings, frames and flooring.
You can use tilt-slab or tilt-up construction on these buildings. This method involves pouring concrete into a wall form and tilting it up to fit in place to form the building's walls. This method is different than precast concrete, which involves pouring the concrete on-site and lifting it into position.
There are additional distinctions between Type lll buildings:
- Group A structures feature walls with fire protection for two hours, while the remainder of the building offers one hour of protection.
- Group B structures also provide two hours of protection from exterior walls, but the rest of the building offers very little resistance, making it possible for flames to spread quickly.
Buildings of this type often feature horizontal void spaces or connected attics, enabling flames to spread unless you install fire stops. The roof systems determine how to ventilate the building. One of the drawbacks of this construction type is that the roof systems can quickly burn, and the fire-cut joists can create a threat to firefighters.
During a fire, the primary goal is to contain the flames within the exterior walls to prevent the fire from spreading to nearby structures. Firefighters can approach these structures by determining whether the building is new or old to establish ventilation decisions. It is possible to accomplish vertical ventilation in these structures. The material combination allows these structures to remain standing if a floor falls. You can find this type of construction in new and older buildings.
You may find more construction options when utilizing this type, but it will provide less fire protection than Type l or Type ll buildings. People often combat this problem by installing high-grade ventilation systems and ceiling sprinklers. These systems connect to the fire alarm system and help slow the spread of flames. This construction type is becoming more common in multi-family construction, and people often opt for fire-retardant-treated wood for construction.
Examples of Type lll buildings may include:
- Single-family homes
- Schools
- Single-story businesses
- Small commercial structures
4. Type lV — Heavy Timber or Mass Lumber
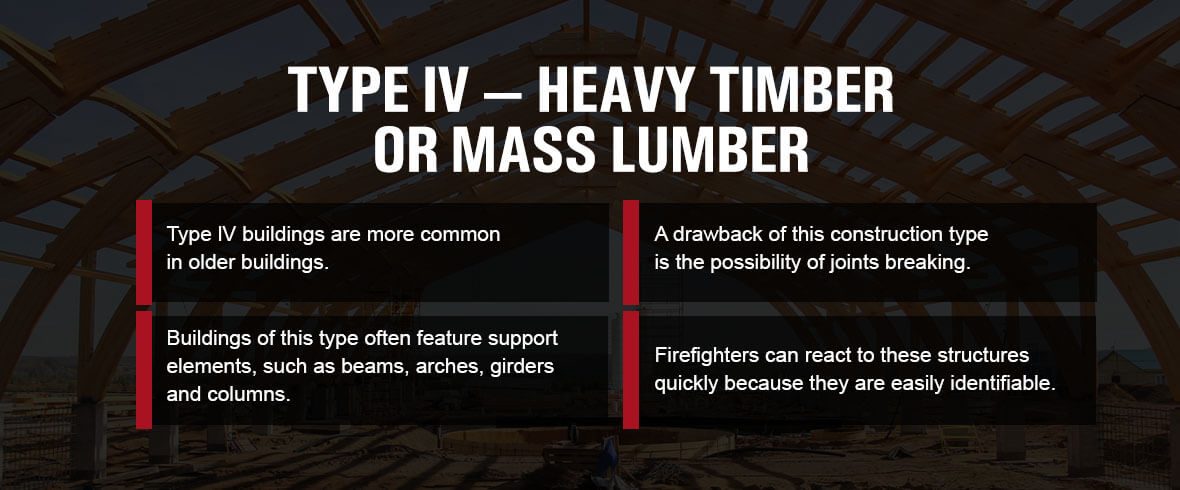
Type lV buildings are more common in older buildings. This type often uses large lumber pieces to complete construction. Firefighters can usually quickly identify these structures because they feature wooden walls or the type of roof span you can find in older factories, barns and churches. The robust structure features metal bolts and plates connecting the lumber. Although these buildings rely on combustible materials, they often fare well in fires because of their lumber size.
This type usually uses laminated or solid wood for construction, with all wooden members meeting necessary dimensional requirements. Buildings of this type often feature support elements, such as beams, arches, girders and columns. These elements are typically at least eight inches thick to encourage durable construction. Additionally, roofs and floors typically feature planks with a thickness of at least six inches. There may be some inflammable walls present in these buildings.
Strengths of this construction type include their load-bearing walls and drainage systems. Load-bearing walls are often non-combustible, and the drainage systems empower responders to water the structure without risking collapse due to increased weight because the water can flow right out of the building.
A drawback of this construction type is the possibility of joints breaking. In high temperatures, metal joints can break, and in some locations, such as older factories with goods, machinery or oil, this can enhance the fire severity. Additionally, although these buildings can often withstand fires without collapsing, other factors could breach the structure's integrity. For instance, weather damage or termites could cause structural damage to the building, leading it to collapse during a fire.
These buildings require a significant amount of water in the event of a fire due to the amount of combustible materials. Keep in mind that these structures often do well because they are very durable, limiting collapses. This means Type lV is an excellent choice if you're looking for a wood-framed building with enhanced fire protection. However, these buildings will be more expensive to complete compared to Type V buildings.
Firefighters can react to these structures quickly because they are easily identifiable. The enhanced durability of heavy timber allows people more time to escape the building and responders to enter and exit in emergencies. Firefighters will rely on large amounts of water to put out the flames. Additionally, sprinkler systems can help extinguish these fires due to the longer burn time.
Examples of Type lV construction could include:
- Old churches
- Aged factories
- Old barns
5. Type V — Wood-Framed
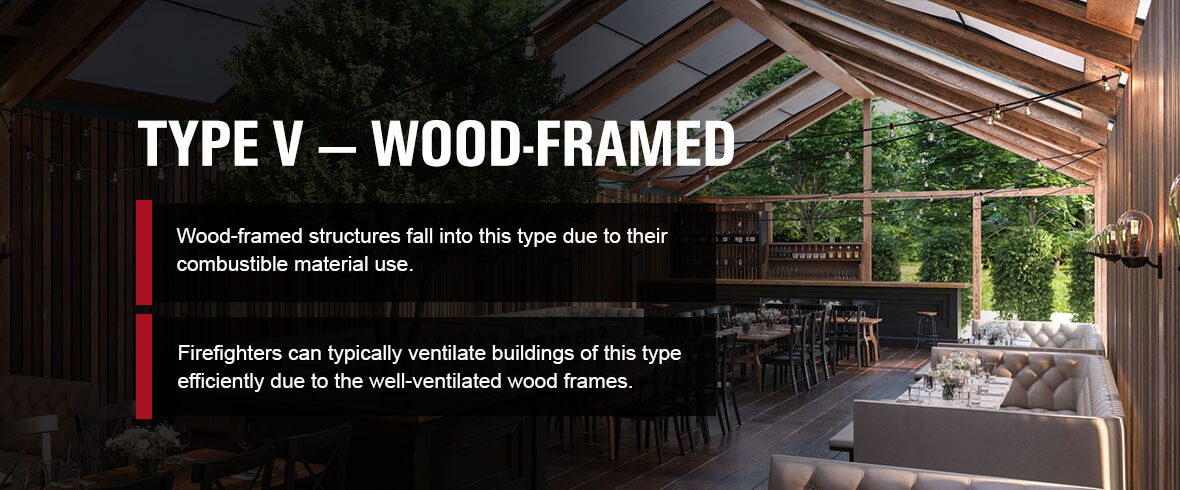
Wood-framed structures fall into this type due to their combustible material use. This category allows you to use any materials with code approval to create the structure. This type does not require any materials to have a fire-resistance rating. This means these buildings are the most combustible, making them most likely to experience severe fire damage.
Many modern homes and single-story facilities are Type V construction. This building type uses manufactured or lightweight wood rather than the heavy timber of Type lV buildings. This material is often inexpensive, structurally sound and efficient but does not offer much fire resistance, allowing these buildings to collapse within minutes.
Often, this type will craft walls, frames, roofs and floors with wood. These pieces may be partially or entirely made from wood. Due to the wood usage, these buildings have no fire resistance and can ignite significantly. However, the lightweight, wooden construction makes these structures a cheaper alternative to others on this list. New building materials are a rising trend in the construction industry, and many have additional valuable properties to enhance structures.
These buildings will typically have structural support to prevent the building from collapsing. Interior platforms can prevent fire from spreading vertically. Additionally, drywall can briefly protect some structural elements, but other materials known in this construction can fuel the fire. These buildings will offer one hour or less of fire resistance, so using non-combustible materials where possible can enhance safety.
Firefighters can typically ventilate buildings of this type efficiently due to the well-ventilated wood frames. However, wood-framed roofs increase the possibility of a flashover or collapse. Additionally, although ventilation can aid firefighters, it can also help the fire spread faster throughout the building. Furthermore, these buildings can challenge responders because the exposed wood won't offer fire resistance. To prevent some of these issues, you can opt for large timber components for primary structural elements to reinforce the structure and minimize the risk of collapse.
These buildings are always smaller than others on the list. Although your project may not require the use of a sprinkler system, you should implement one to enhance safety.
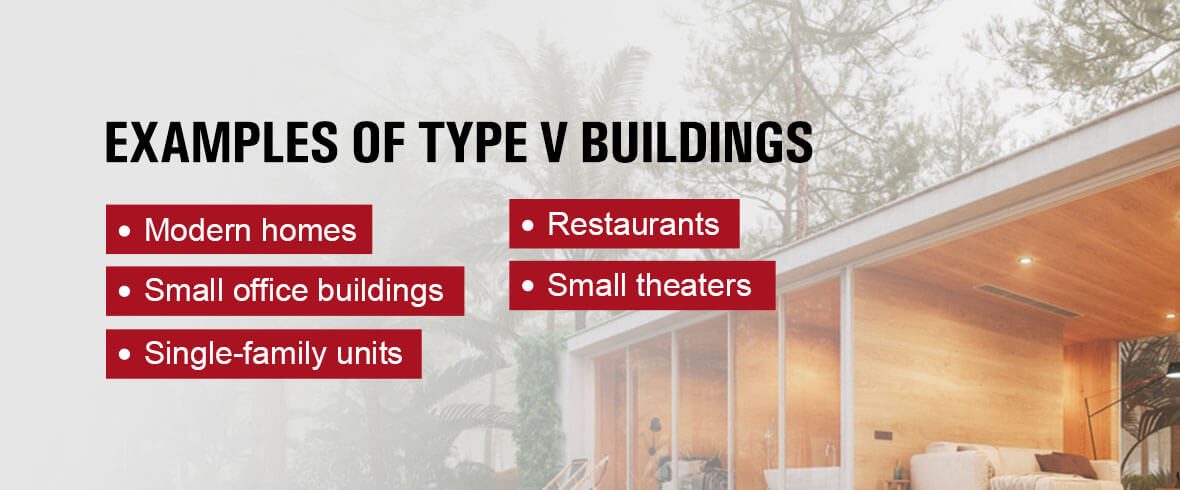
Examples of Type V buildings include:
- Modern homes
- Small office buildings
- Single-family units
- Restaurants
- Small theaters
Deciding Which Building Construction Type You Need
Local laws and building codes often feature regulations regarding the construction type you can choose. Assembly space buildings will have different requirements than multi-family housing units or public shopping facilities. Always evaluate local codes to determine what construction type you must utilize.
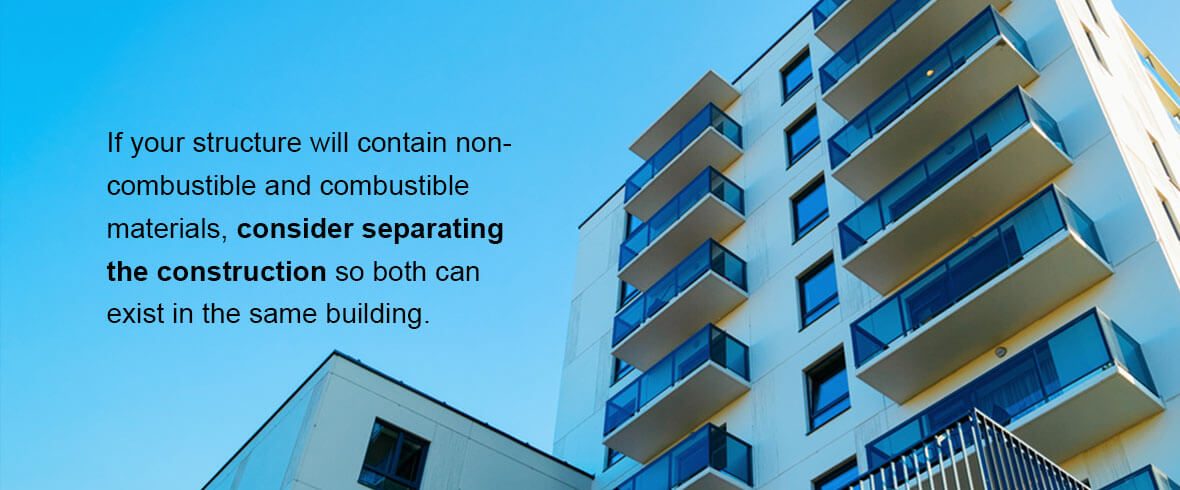
If your structure will contain non-combustible and combustible materials, consider separating the construction so both can exist in the same building. You can create a firewall to create two fire areas. Some shopping centers and similar settings utilize this design. For example, a grocery store may require non-rated steel, while an adjacent retail location has different requirements. To mitigate potential damage, you can construct a firewall with concrete blocks between the two.
Keep in mind that some structures will require a specific building construction type. For example, a multi-level hospital will need a Type 1 Group A design for its facility. These projects will highlight whether the construction type is crucial to the project. Additionally, be sure you can meet construction deadlines with the type you choose.
Another consideration to showcase which type is best for your project is the cost. Whether you're working on an independent project or have a unique client, you must consider the overall project total. Often, you can expect to pay more for buildings with more fire resistance. This means some construction types may be unsuitable for some projects. However, this also means you may be able to opt for a more resistant construction type if you're working on a smaller project with a large budget.
Ultimately, understanding the building's purpose, building codes, common environmental factors, local codes and the project budget will determine which building type is right for you.
Find Construction Equipment From The Cat® Rental Store
Understanding the different building construction types is essential for completing a successful project. Your knowledge of each type will provide deep insight into what you can accomplish and whether your structure will provide the safety and fire resistance your requirements demand. However, knowledge is only one part of the job. You also need reliable and high-quality equipment to complete successful projects.
The Cat® Rental Store has the equipment you need, regardless of your industry, including utilities, landscaping, general construction, residential or commercial building, road building or industrial manufacturing. With us, you can find what you need to get the job done right. We offer items like construction equipment, concrete saws and everything in between for a comprehensive catalog of everything your job demands.
Our safe, reliable products utilize the latest technologies so that you can feel confident in every purchase. We also offer operator training, expert advice and on-site support so that you can always find the resources you need to carry a project from start to finish successfully.
No matter what you're looking for, you can find it with us. We offer thousands of work tool attachments and machines from one of the most respected manufacturers. Our extensive inventory features products from over 70 leading allied companies with reputations for safety, reliability and quality. You won't find such a vast selection anywhere else. Browse our equipment to find the right pieces for your next job. Rent whatever you need from people who do whatever it takes.