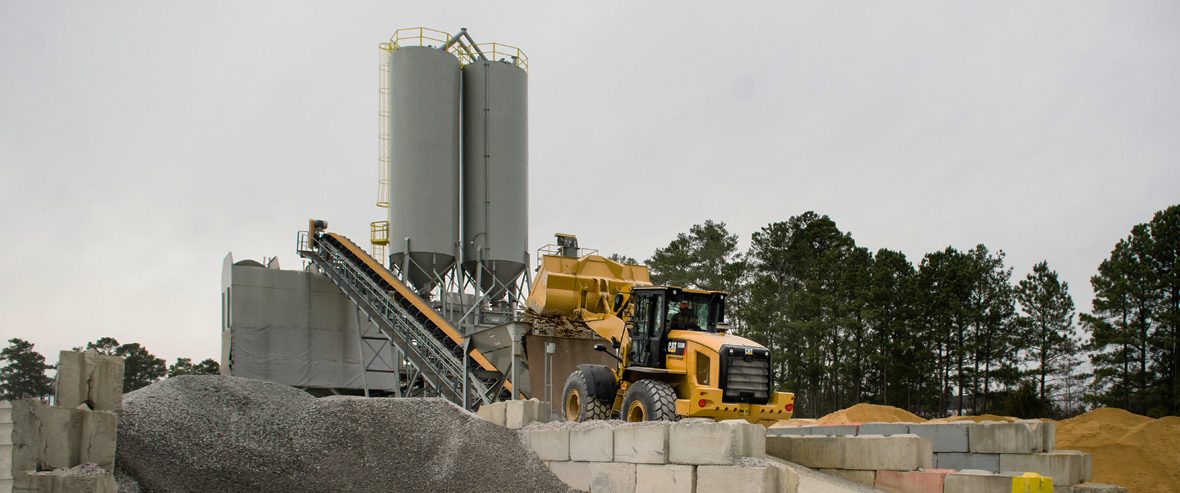
The Concrete-Making Process
Concrete is an essential building material that keeps our world together — from pathways to patios to building construction, concrete is used for a variety of crucial projects you use daily.
Modern concrete is a mixture of sand or gravel, also referred to as aggregate, Portland cement and water that is poured into a mold. When evenly distributed and exposed to air, the liquid concrete hardens into a solid structure. While the concrete making process may seem like a straightforward task, there are several factors to consider when mixing your concrete to achieve a successful, durable and attractive finished product.
How Is Concrete Made
For every building project, a specific concrete mixture is determined — the key to a strong concrete is its composition, or the proper proportion and mixture of the water, aggregate and other ingredients. Concrete mixture quality is largely determined by the cement paste and the aggregate and water ratio.
Mixtures that don’t have enough paste to fill the spaces between the aggregates will be difficult to form and will have a rough, porous surface, and those with too much paste will be easier to handle with a smooth surface, but can easily crack under certain conditions. Typically, properly mixed concrete will have 10 to 15 percent cement, 60 to 75 percent aggregate like sand or gravel and 15 to 20 percent water for proper durability and long-term strength.
When mixing large batches of concrete, take the following steps to ensure proper results:
- Design the concrete mix: When determining the proper mixture of cement, aggregate, and water, it’s best to consider the final use for the concrete and several factors including the expected supporting load requirements of the cement, whether the concrete needs to be poured, pumped or sprayed, the local environment and the expected surface wear.
- Send mix to batching plant: Most concrete loads, large and small, are batched and mixed at a central batching plant, then trucked to their final location. These plants have a variety of aggregate and cement options that are stored in controlled environments, ready to be properly weighed and thoroughly mixed for a higher quality final product.
- Mix and pour concrete: For the best results, the concrete materials must be thoroughly mixed with proper equipment so it evenly distributes the aggregates throughout the cement paste and is evenly saturated by the water, breaking up clusters. After the concrete is completely mixed, it can be placed into a formed mold to complete its final shape using a truck or buckets.
- Consolidate: After the concrete is in place, it must be consolidated using specialized tools to remove any air bubbles that could compromise the overall structure of the concrete.
- Finish and cure materials: For concrete flooring and pavement, the concrete must be finished with a specific treatment — either screening, floating or troweling — to ensure lasting appearances and durability. Once it’s been finished, the concrete’s curing process can begin, which requires proper support and moisture. The concrete should be covered with plastic or a damp cloth to prevent evaporation and be allowed to fully gain strength and harden over the next few hours.
Browse concrete equipment.
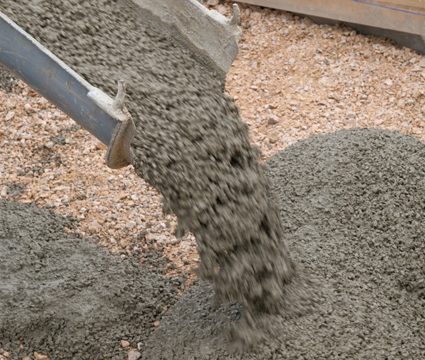