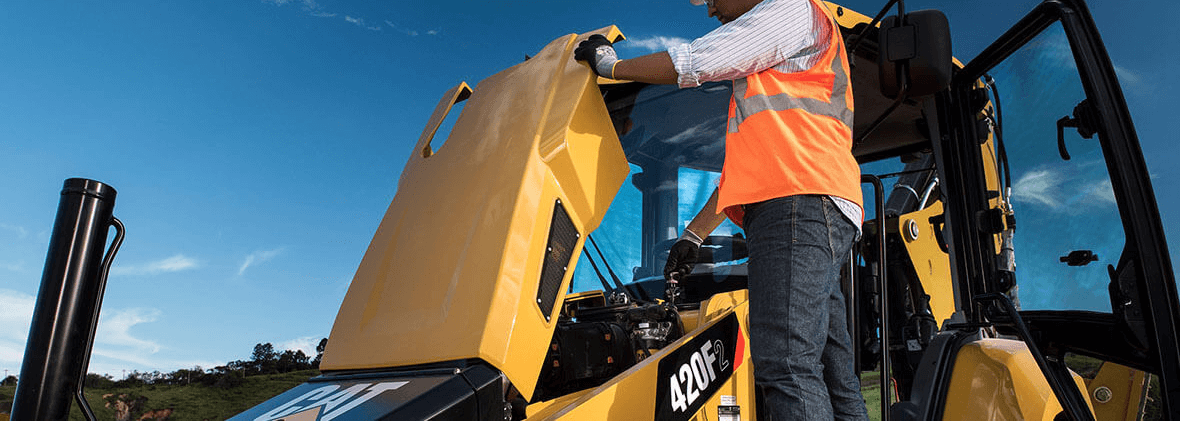
Maintenance Tips for Prolonged Use of Your Rented Equipment
Renting large equipment offers a cost-effective solution for any task or project. Whether you're using heavy machinery, construction equipment or industrial tools, proper maintenance is crucial to ensure the equipment's optimal performance and safety throughout extended rental periods. This guide provides comprehensive maintenance tips to help you maximize the efficiency and longevity of your rented large equipment.
Jump to a section:
Benefits of Proper Maintenance for Rented Equipment
When it comes to large machinery and industrial tools, consistent upkeep offers several benefits that impact performance, safety, budget, compliance and overall longevity.
Enhanced Performance
Regular maintenance directly contributes to the enhanced performance of heavy equipment. Clean, lubricated and adequately calibrated machinery operates at its optimal capacity, ensuring smoother operations, improved efficiency and minimal downtime.
Well-maintained equipment can handle tasks more effectively, resulting in increased productivity and the timely completion of projects.
Enhanced Safety
Safety is paramount in any work environment, especially when dealing with heavy machinery. Proper maintenance significantly reduces the risk of equipment failures, malfunctions or accidents that could endanger operators and bystanders. Regular inspection and repairs ensure that safety mechanisms, like emergency stop buttons and warning indicators, are functional.
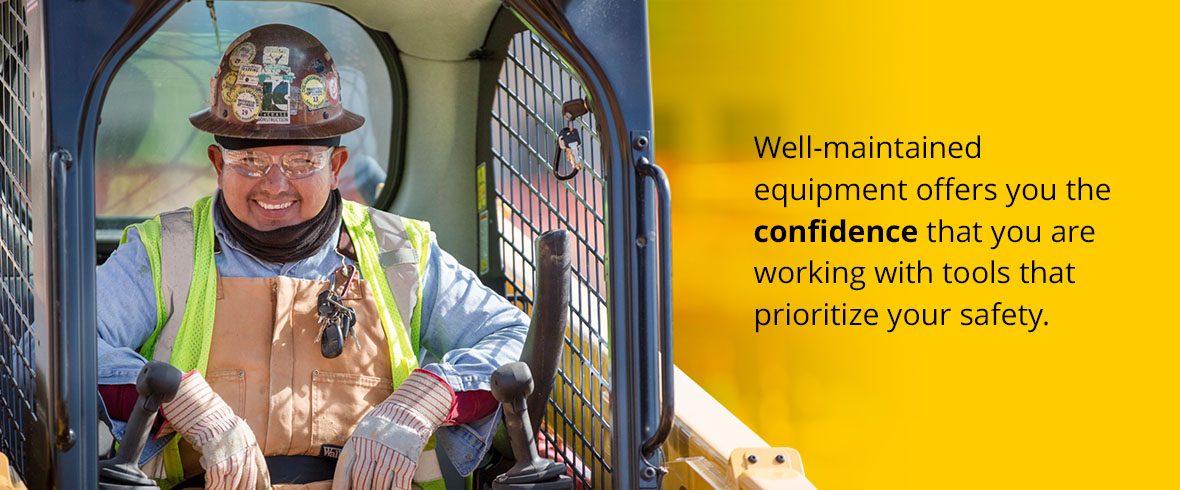
Well-maintained equipment offers you the confidence that you are working with tools that prioritize your safety.
Cost Savings
Although maintenance may seem like an additional cost, it is a wise investment that can provide you with substantial cost savings in the long run. Addressing minor issues promptly prevents them from escalating into significant problems that require expensive repairs or replacements.
Downtime due to unexpected breakdowns can result in project delays and increased labor costs. A well-maintained machine is less likely to experience sudden failures, reducing unplanned downtime and its associated financial implications.
Compliance
Many industries have regulations and standards in place to ensure the safe and effective operation of heavy equipment. Proper maintenance practices help you stay compliant with these regulations. Regular inspections, maintenance routines and documented records demonstrate your commitment to safety and adherence to industry guidelines. Compliance helps avoid potential legal issues and promotes a culture of responsibility within your organization.
Extended Life Span
Every piece of heavy equipment has a finite life span, but proper maintenance can significantly extend its operational life. Regular upkeep helps prevent premature wear and tear, corrosion and other factors that contribute to equipment deterioration. By consistently addressing minor problems and performing necessary repairs, you can maximize the return on your investment and keep equipment functional for more extended periods.
14 Maintenance Tips for Rental Heavy Equipment
Maintaining rented large equipment is a matter of operational efficiency and a critical aspect of safety and cost-effectiveness. When you properly and regularly care for your equipment, you ensure less downtime and reduce breakdown risk while maximizing the return on your rental investment. Here are maintenance tips for rental equipment you can follow to ensure your operations run smoothly.
1. Follow Manufacturer Guidelines
It's crucial to always keep your equipment manufacturer's manual on hand. This document provides valuable insights into operating procedures, maintenance requirements and safety guidelines specific to your equipment.
Adhering to the manual's guidelines can provide the following benefits:
- Prevent premature wear and tear: You'll also want to familiarize yourself with the equipment's components and mechanisms to help you identify potential issues. Regularly inspect moving parts, hydraulic systems, electrical connections and any sensitive areas to prevent wear and tear.
- Employ the recommended maintenance schedule: Following the recommended maintenance schedule can ensure you're giving your specific equipment the proper amount of maintenance to ensure it works properly.
- Safeguard your equipment's functionality: The manufacturer's manual helps users preserve the integrity of their equipment while minimizing risks and ensuring optimal performance throughout its lifecycle.
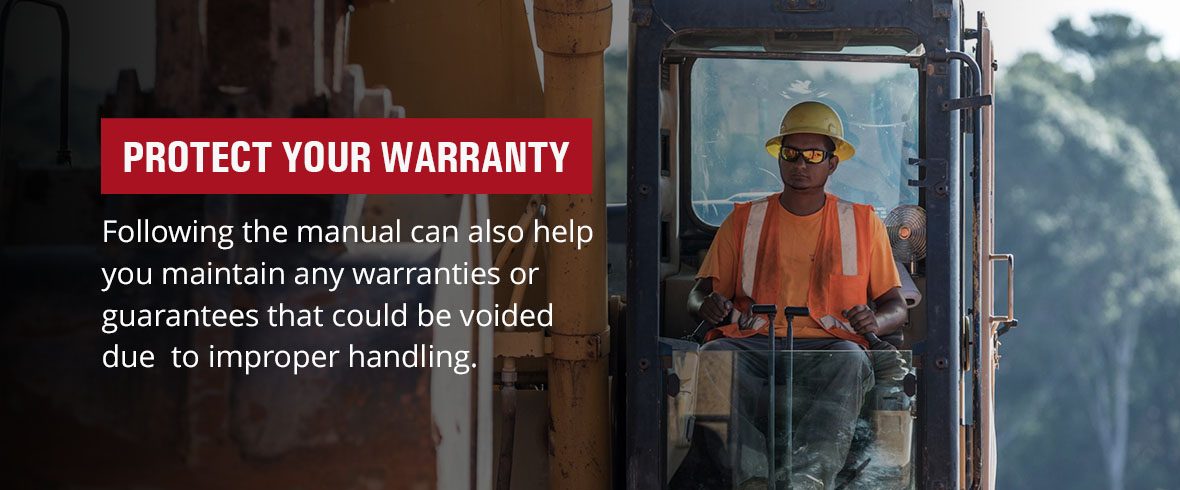
- Protect your warranty: Following the manual can also help you maintain any warranties or guarantees that could be voided due to improper handling. You'll often find troubleshooting tips in the manual, aiding in problem-solving without resorting to unnecessary experimentation.
2. Regularly Clean and Remove Debris
Regularly cleaning and removing debris from your equipment is a fundamental aspect of maintenance that can't be overlooked. Accumulated dirt, dust and debris can compromise the equipment's performance and efficiency, potentially leading to breakdowns or costly repairs. Effective cleaning prevents the clogging of vital components, such as filters and cooling systems, which can impact the equipment's overall functionality.
Following a consistent cleaning routine can provide the following benefits:
- Identify wear and tear: Cleaning your equipment correctly can help operators discover signs of wear and tear more easily, enabling timely interventions to prevent further damage.
- Reduce the risk of corrosion and rust: Regularly cleaning your equipment can also reduce the risk of corrosion and rust from developing, extending your equipment's life span.
- Prevents potential hazards: Well-maintained equipment operates more smoothly, consumes less fuel and adheres to safety regulations — mitigating potential dangers in the workplace.
Implementing a regular cleaning schedule into your maintenance regimen enhances the equipment's longevity and minimizes downtime, optimizes performance and ultimately helps save on repair costs.
3. Consistently Monitor Fluid Levels
Monitoring your equipment's fluid levels is a critical practice for effective maintenance. Fluids, such as oil, coolant, hydraulic fluid and transmission fluid, keep the machinery running smoothly and prevent overheating and wear. Regularly checking and maintaining proper fluid levels is crucial for optimal performance and longevity.
By consistently monitoring fluid levels, operators can:
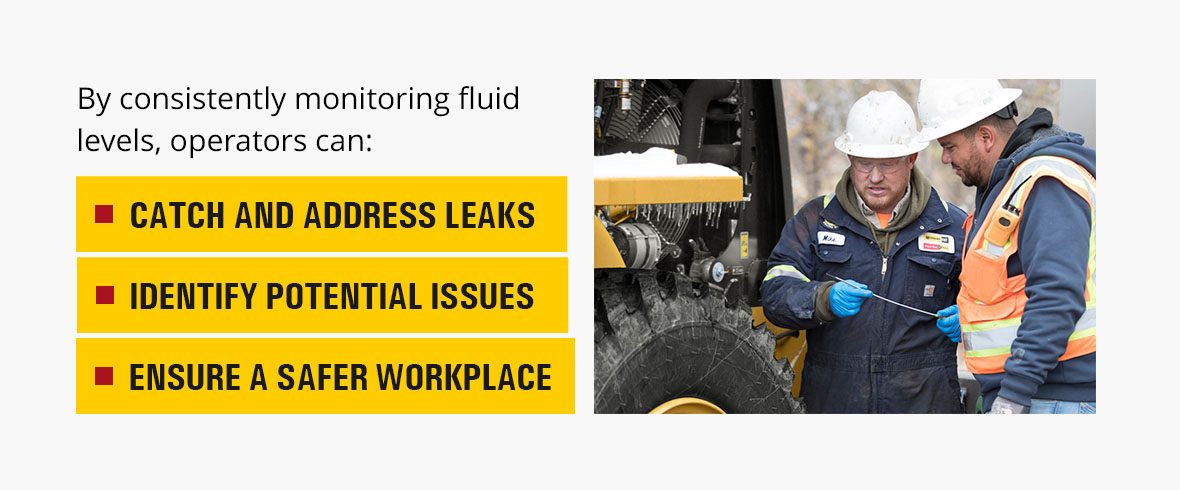
- Catch and address leaks: Insufficient fluid levels can lead to increased friction, heat and wear, causing components to break down prematurely. Conversely, overfilling can lead to leaks, reduced efficiency and potential damage. Monitoring fluid quality alongside levels is equally crucial, as contaminants can accumulate and compromise the fluid's effectiveness.
- Identify potential issues: This proactive approach can help prevent catastrophic failures, reduce downtime and extend your equipment's life span.
- Ensure a safer workplace: Additionally, adhering to fluid maintenance guidelines outlined in the manufacturer's manual maintains warranties and ensures compliance with safety standards — promoting a safer and more efficient work environment.
4. Regularly Grease Moving Parts
Regularly greasing moving parts is a pivotal practice in equipment maintenance that promotes optimal functionality and durability. Here are a few benefits of lubricating these components:
- Maintains your equipment's performance: Without proper lubrication, moving parts can generate excessive heat and friction, leading to premature wear and potential safety hazards. Follow your manufacturer's recommendations to grease each piece properly. You'll maximize your equipment's productivity and be able to identify wear patterns, leaks or other issues during the maintenance process.
- Reduces energy consumption: Adhering to manufacturer-recommended greasing intervals, as specified in the manual, can also reduce your equipment's energy consumption — ultimately contributing to a more efficient and cost-effective operation.
- Extends your equipment's operational life: Moving parts, like bearings, joints and gears, require proper greasing to operate smoothly and efficiently. Greasing these crucial components consistently can ensure they remain well-lubricated and protected from corrosion, reducing the likelihood of breakdowns and costly repairs.
5. Avoid Overloading and Misuse
Sensible operation by avoiding overloading and misuse is crucial for maintaining your heavy equipment. Overloading strains components beyond their designed capacity, hastening wear and tear and increasing the risk of catastrophic failures. Misuse, such as operating equipment outside its intended purpose or disregarding operation guidelines, can lead to premature damage and compromised safety.
Here's how you can avoid overloading and misuse:
- Follow the manual: Always adhere to load limits, usage guidelines and safety protocols outlined in your manufacturer's manual. Respecting weight capacities, speed limits and terrain suitability can ensure your equipment lasts longer and minimizes the likelihood of accidents.
- Invest in operator training: Regular training for operators on correct usage practices can help prevent unintentional stress on critical parts. Ultimately, responsible operation extends your equipment's service life, maximizes return on investment and fosters a safer and more efficient work environment.

By avoiding overload and misuse, you safeguard both your equipment and personnel. The approach prevents unnecessary strain, reduces repair costs and sustains peak performance.
6. Train Operators for Proper Usage
Adequately trained operators possess the skills to handle equipment correctly, minimizing the risk of accidents, premature wear and costly repairs. Comprehensive training equips you with an in-depth understanding of the equipment's intricacies, allowing you to detect early signs of malfunction and perform routine maintenance tasks. More benefits include:
- Optimized workplace efficiency and productivity.
- Identification of operational inefficiencies.
- Employ best practices to ensure smooth functionality — ultimately extending the equipment's life span.
- Promote a safety-conscious mindset, reducing workplace incidents and fostering a secure work environment.
- Enhances equipment performance and your return on investment.
By fostering expertise, companies create a culture of care and responsibility, reducing downtime, repair expenses and potential legal liabilities. The dividends include prolonged equipment life, improved operational output and a workforce proficient in safeguarding assets through proper equipment usage and maintenance.
7. Schedule Regular Inspections
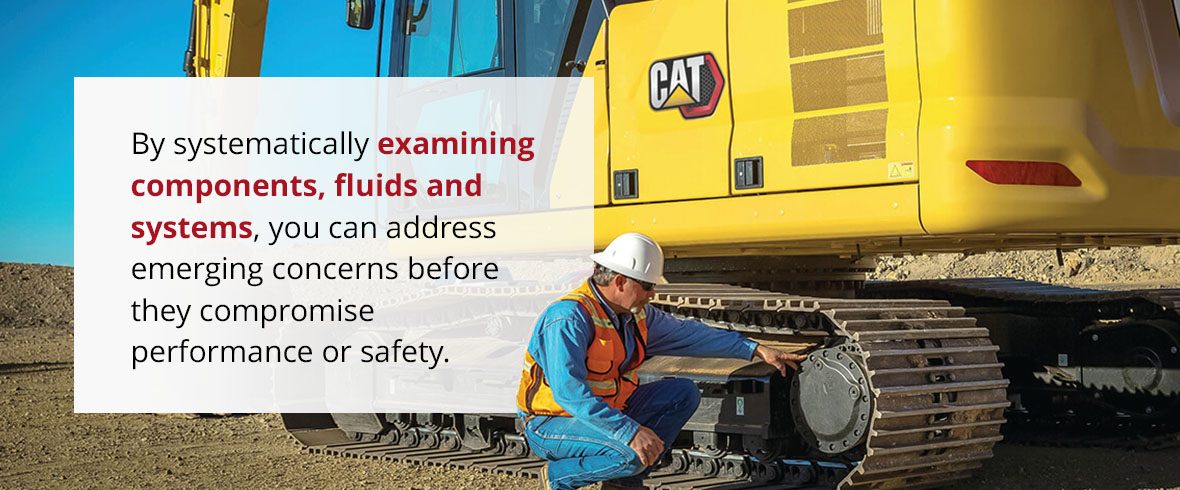
Regular inspections are a cornerstone of effective equipment maintenance. Scheduled inspections allow you to quickly identify wear, damage or potential problems before they become major breakdowns. By systematically examining components, fluids and systems, you can address emerging concerns before they compromise performance or safety.
Inspections can also provide advantages like:
- Correct maintenance intervals: Facilitating adherence to manufacturer-recommended maintenance intervals ensures your equipment can operate within optimal parameters.
- Identify wear and tear: Timely checks also help you find irregular patterns or signs of wear, allowing you to make quick adjustments or replacements.
- Planning and resource allocation: Additionally, inspections provide valuable data for predictive maintenance, enhancing planning and resource allocation.
- Cultivate responsibility: Frequent inspections also cultivate a culture of vigilance and accountability, allowing you to minimize downtime and repair costs. Such proactive efforts can extend your equipment's life span and contribute to a safer work environment.
Regularly scheduled inspections form a critical foundation for well-maintained equipment, improving reliability, maximizing efficiency and safeguarding both assets and personnel.
8. Identify Wear and Tear
Identifying wear and tear is a crucial aspect of heavy equipment maintenance. Regular visual assessments aided by proper training can help you recognize signs of deterioration, such as worn-out components, leaks or unusual noises. Monitoring your equipment's performance metrics and comparing them against benchmarks can highlight deviations that signify underlying problems.
You can identify wear and tear using the following strategies:
- Implement technology: Incorporating advanced technologies like vibration analysis and thermography enables a more in-depth understanding of wear patterns.
- Monitor fluid quality: Monitoring fluid quality and levels is also crucial, as contaminants or low levels can accelerate wear.
- Track maintenance history: Additionally, you should track your equipment's maintenance history and compare it to manufacturer guidelines, as this can help you recognize trends and anticipate component failures.
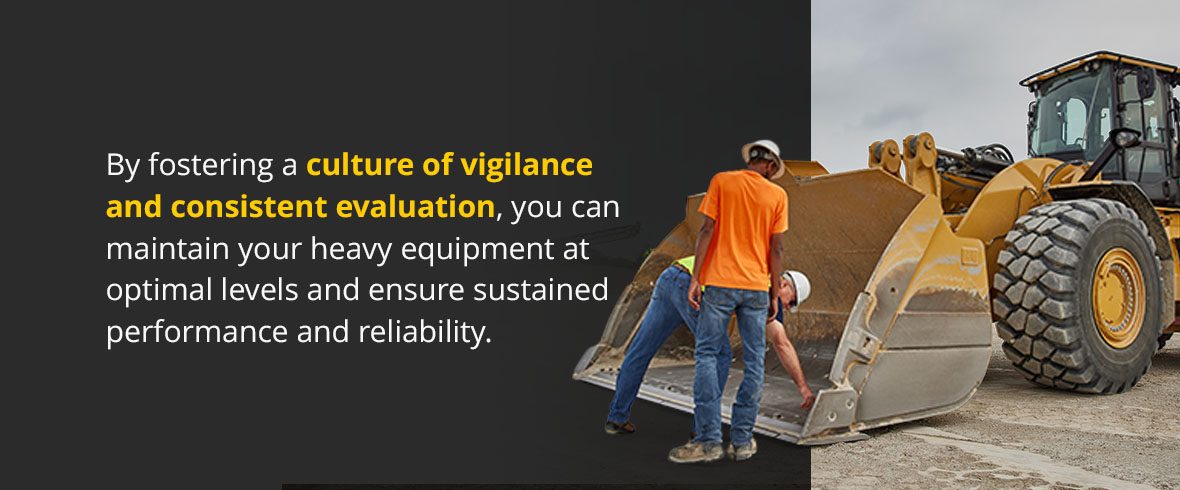
Proactive wear and tear identification empowers you to address issues before they escalate into significant problems. This practice can minimize costly downtime, extend your equipment's life span and enhance operational safety. By fostering a culture of vigilance and consistent evaluation, you can maintain your heavy equipment at optimal levels and ensure sustained performance and reliability.
9. Address Minor Issues Promptly
Addressing smaller issues quickly is a crucial aspect of effective heavy equipment maintenance. Minor issues, if left unattended, can escalate into larger, more costly complications that result in extended downtime and substantial repair expenses. Here are a few benefits of quickly addressing minor issues:
- Prevent failures: Addressing minor problems can prevent a domino effect and its impact on adjacent components and systems. Proactively resolving these issues helps maintain the integrity of your equipment's operation, preventing more significant failures that could disrupt workflow and pose safety hazards.
- Maximize productivity: Timely intervention can prevent minor issues from compromising your equipment's overall performance and efficiency. By promptly addressing minor issues, you can maximize your productivity and return on investment.
- Promote safety: Regular maintenance checks and immediate corrective actions ensure equipment operates at peak efficiency, reducing the risk of unexpected breakdowns and contributing to a safer work environment.
Prioritizing solving minor concerns is an integral part of maintenance, leading to a longer equipment life span and optimized performance.
10. Make Proper Machine-Specific Adjustments
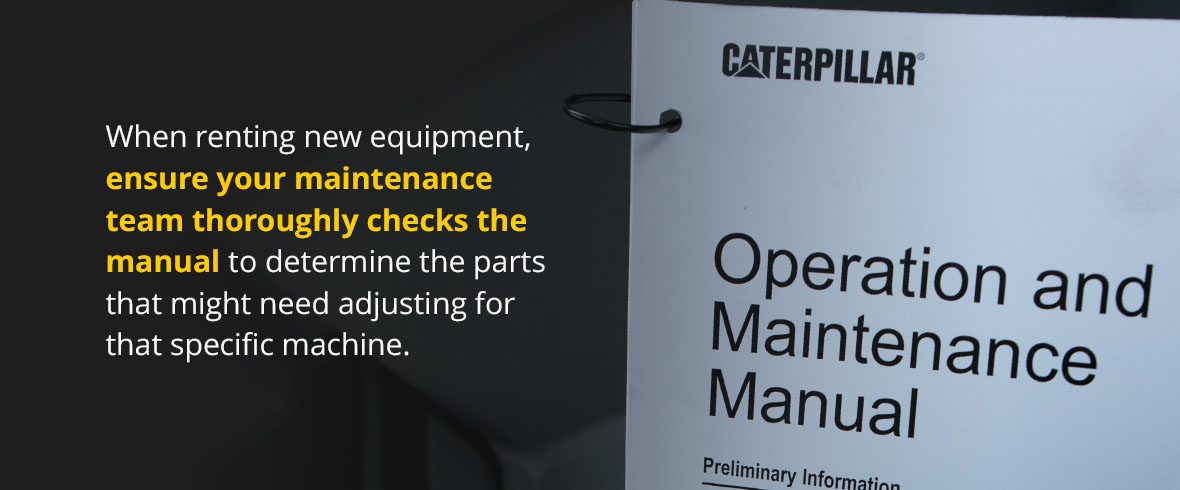
Each piece of equipment comes with a different set of adjustments. Without making the correct machine-specific adjustments, you risk equipment malfunction. When renting new equipment, ensure your maintenance team thoroughly checks the manual to determine the parts that might need adjusting for that specific machine.
For instance, you might make wheel alignment adjustments for trucks and other machines with wheels. If not correctly aligned, your equipment can have difficulty steering and handling, which can extend the tire wear and increase fuel consumption. Over time, this can lead to breakdowns. As a result, you'll want to check your alignment when getting a new tire and changing one or more steering components.
Following machine-specific adjustment guidelines can help you ensure everything is aligned correctly and ready for any project that comes your way. No matter the specific adjustment, you should follow a consistent schedule for them. That way, you can promote a safer, more efficient workplace.
11. Be Prepared for Unexpected Breakdowns
No matter how diligently you maintain your equipment, breakdowns can still occur due to factors beyond your control. Being prepared for such situations is crucial. Develop an emergency response plan that includes steps to take when a breakdown occurs. This might involve:
- Having spare parts on hand.
- Establishing communication protocols with your maintenance team.
- Having a clear process for reporting breakdowns.
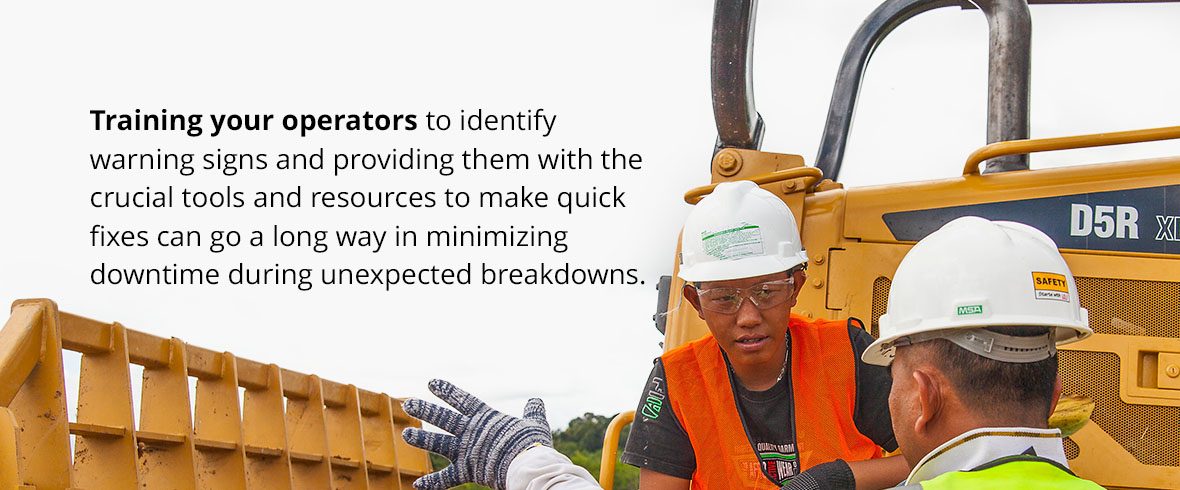
Regularly inspecting your equipment and addressing minor issues promptly can reduce the risk of major breakdowns. Training your operators to identify warning signs and providing them with the crucial tools and resources to make quick fixes can go a long way in minimizing downtime during unexpected breakdowns.
12. Reach Out to Your Rental Company for Support
Your rental company can be an invaluable resource for maintenance support. Rental companies often have a team of technicians and mechanics well-versed in the equipment they provide. They can offer guidance on proper operation, routine maintenance and troubleshooting to reduce downtime associated with breakdowns.
A reputable rental company will offer expertise, provide solutions and even dispatch technicians to your site if needed. Leveraging the support from your rental company enhances your ability to maintain the equipment effectively, even if you're unfamiliar with the machinery's intricacies.
13. Ensure Proper Storage and Parking
Proper storage and parking are essential aspects of heavy equipment maintenance that are often overlooked. When equipment is not in use, you should store it in a secure and designated area. The area should be level and free of debris, ensuring your equipment remains stable and protected.
Whenever possible, park your equipment under cover to shield it from the elements. Exposure to sun, rain, snow and wind can accelerate wear and corrosion, potentially leading to premature deterioration. Proper storage extends the equipment's life span and reduces the frequency of maintenance tasks required to counteract weather-related damage.
14. Protect Equipment From Weather
The weather can significantly impact heavy equipment, causing gradual wear and even sudden malfunctions. To prevent this, invest in weather protection measures that safeguard your machinery from adverse conditions:
- Sun: Prolonged exposure to the sun's ultraviolet rays can cause paint to fade, rubber to crack and plastic to deteriorate. Use tarps and covers or park your equipment under shaded structures to reduce sun exposure.
- Rain and moisture: Moisture can lead to rust, corrosion and electrical problems. Cover your equipment with waterproof covers or park it in a dry area to prevent water from accumulating on surfaces and components.
- Snow and ice: Snow and ice can cause moving parts to freeze, potentially damaging them. To prevent this, clear off snow and ice before starting the equipment and consider using heaters or de-icers to melt accumulated ice.
- Wind: Strong winds can dislodge loose parts or debris, causing damage. Park your equipment away from loose materials, secure loose items and consider using windbreaks or barriers to minimize the impact of strong winds.
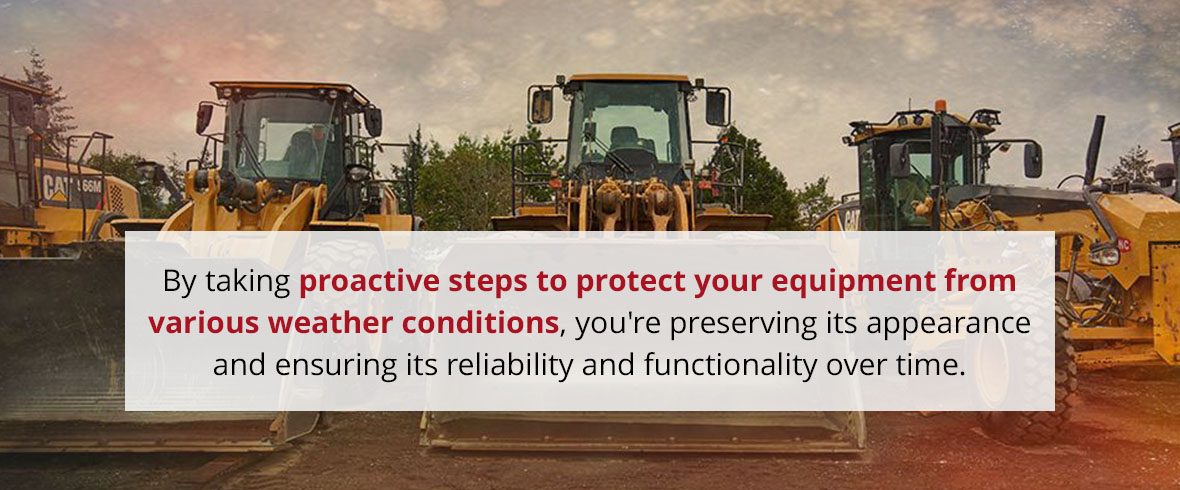
By taking proactive steps to protect your equipment from various weather conditions, you're preserving its appearance and ensuring its reliability and functionality over time.
Get Top-Quality Equipment at The Cat® Rental Store
Maintaining your heavy equipment involves proactive planning, regular inspections, effective communication and protective measures. Following manufacturer guidelines, identifying wear and seeking support from rental companies are all crucial strategies for keeping your machinery in optimal condition.
If you're looking to rent heavy equipment, look no further than The Cat® Rental Sore. We provide an extensive selection of top-quality equipment and tools for rent for various industries. Our rentals are well-maintained, ensuring optimal performance to increase your productivity and promote a safe work environment.
Visit a Cat dealer near you or call 1-800-RENT-CAT today to get started.