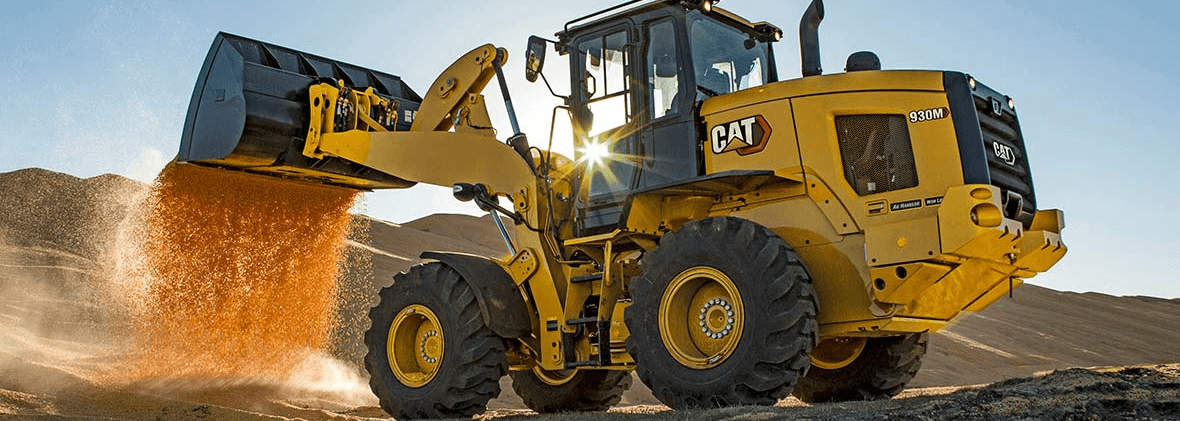
How Rental Equipment Can Fill the Gaps During Equipment Maintenance
Downtime is any company’s major obstacle to overcome. During downtime, your business is not making money, and it may even be losing money due to the many costs associated with equipment being idle. Some of the significant operating costs associated with downtime include:
- Repair and maintenance costs, including technician labor and part replacements
- Rental equipment costs and time spent learning new machinery
- Employee wages that need to be paid while the equipment is idle
- Potential penalties for failing to meet production milestones
All businesses that rely on equipment expect that they’ll experience downtime — both planned and unplanned. In order to prevent downtime from interfering with productivity, you can rely on equipment rentals to fill the gaps so you can keep up with production.
Jump to a section:
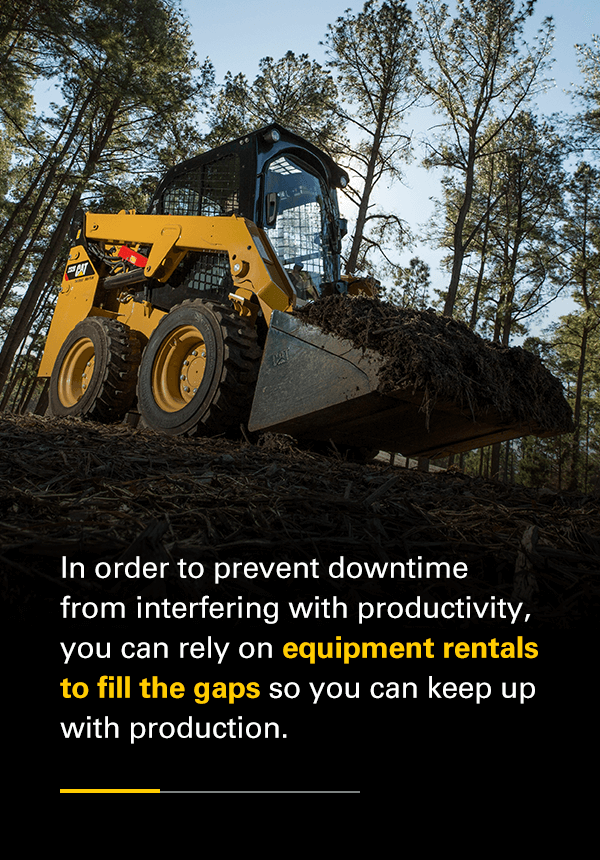
Renting Equipment to Reduce Downtime
Across the construction industry, different companies aim to keep downtime as minimal as possible. Downtime is your equipment’s time spent being unproductive during what are considered its productive hours. You need a strategy that plans for downtime and allows your team to swiftly implement a solution to compensate for the equipment being idle.
Having a contingency plan is crucial. You need a quick, convenient and effective equipment solution to fill in the gaps during planned and unplanned downtime. Having access to on-demand equipment rentals is valuable for reducing downtime and maintaining tight production schedules. It also gives you greater control over your downtime costs by providing reliable equipment to stay productive or get up and running again.
Planned vs. Unplanned Equipment Downtime
When discussing how renting equipment can reduce downtime, it's important to make the distinction between planned and unplanned downtime. Both scenarios occur in every business. The main difference between the two types of downtime is the level of control you have over each. With planned downtime, you can build the costs into your operating budget. With unplanned downtime, you can’t obtain concrete financial numbers, so you’re left with estimates based on past experience.
The larger the fleet, the greater the risk of unplanned downtime, and the more important planning for downtime becomes. Below is a look at the differences between planned and unplanned downtime, their leading causes and how renting equipment can help mitigate costs in each scenario.
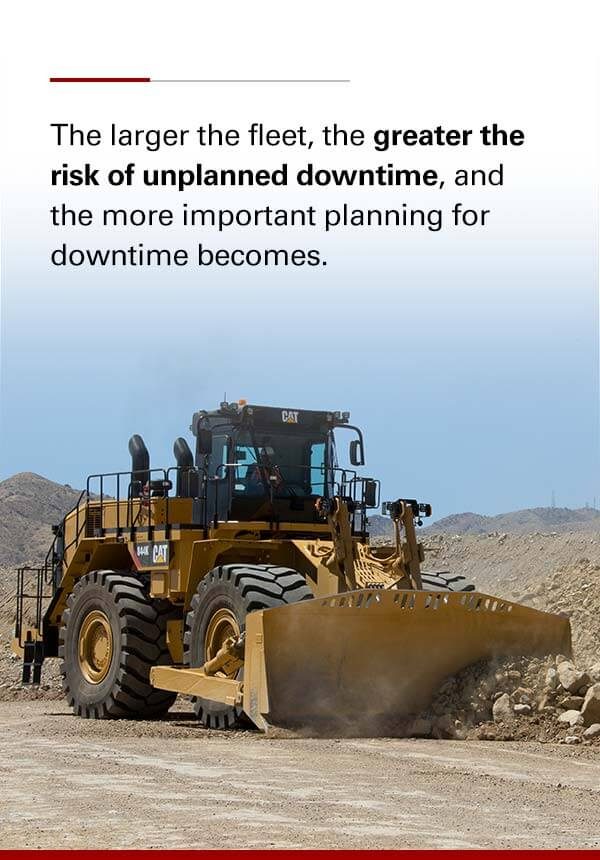
Planned Downtime
Planned downtime is unproductive equipment time that has been scheduled and accounted for financially. Companies use a planned downtime equation to calculate the average cost of scheduled, non-productive time based on the number of hours a machine is expected to be in operation annually.
The most common causes of planned equipment downtime include:
- Transportation: Moving equipment from one project site to another is considered downtime. Because it can be scheduled, it’s known as planned downtime. Though the machine is idle, it’s a necessary cost to incur so the machine can continue being productive at another project.
- Scheduled maintenance: Scheduled or planned maintenance is a necessary cost because it’s what prevents sudden machine breakdowns that stop work in the middle of productive time. Scheduled maintenance is based on servicing intervals as prescribed by the manufacturer, the machine’s operating hours and overall usage rates.
- Work site inspections: Work stoppages can occur for a variety of reasons, but work site inspections are one of the common causes. Scheduled inspections help project managers stay proactive and anticipate problems that would lead to unplanned downtime — thereby mitigating these future costs.
Of these causes of planned downtime, scheduled maintenance has the greatest direct impact on unplanned downtime. Scheduled maintenance allows fleet managers to get ahead of mechanical issues that could eventually cause a breakdown. Having a planned maintenance program is the best way to reduce costly breakdowns and production delays.
The great thing about scheduled maintenance is that you know ahead of time when a machine will be out of service and for how long. This allows project managers to secure a replacement machine in the meantime. Renting equipment during planned downtime prevents any loss in productivity and can easily be budgeted for ahead of time.
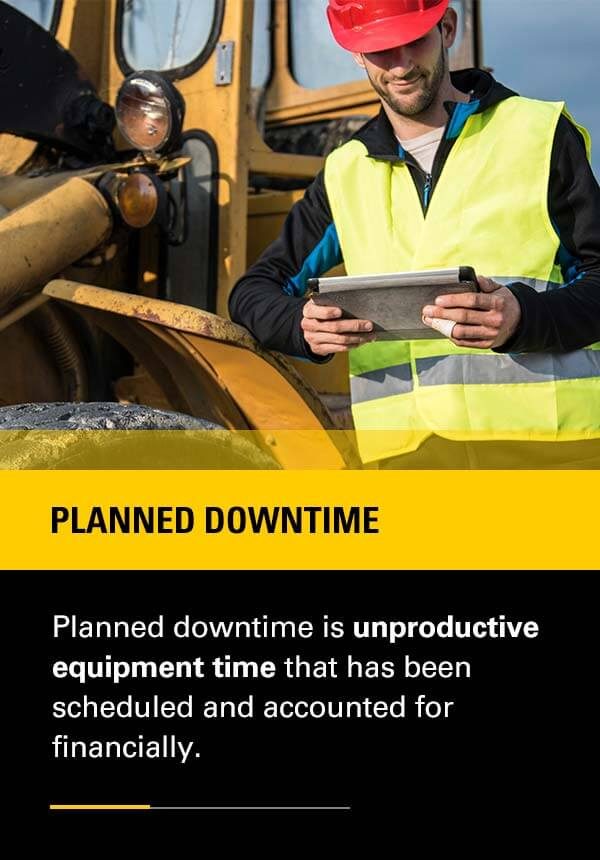
Unplanned Downtime
Unplanned downtime occurs when equipment is out of commission due to an unforeseen or unexpected reason. It’s by far the costlier type of downtime because it cannot be controlled or accounted for in its entirety. As a result, unplanned downtime can derail entire projects in both budget and timeline.
On a construction site, equipment works together as an integrated whole. If one machine is down and can’t perform its job, the other equipment operators who are waiting for certain tasks to be done also get delayed in their productivity. The result is a significant bottleneck that impedes production across the whole project. When a machine breaks down or becomes idle, the entire management schedule needs to be adjusted to account for the delay.
Some of the causes of unplanned equipment downtime include:
- Unexpected breakdowns: Improperly maintained machines break down eventually. Inadequate lubrication, worn-out parts, electrical failures and more can all require immediate servicing before a machine can be used.
- Workplace accidents: A workplace accident halts everything while emergency response or an investigation takes place. This disrupts production and idles machinery in the meantime.
- Weather-related stoppages: Inclement weather patterns, whether it’s heavy rain, snow or wind, can pause productivity. While waiting for the weather to pass, machines sit idle for safety reasons.
Of the above causes, failing to keep up with preventive maintenance is one of the leading reasons for unplanned downtime. This is an unfortunate reality because it’s caused by not implementing or adhering to a preventive maintenance plan. Whether managing a single piece of equipment or hundreds, preventive maintenance is your greatest weapon in defending against unplanned downtime.
When equipment breakdowns occur, it’s essential to be able to rent equipment to fill in the gaps during unplanned downtime. This allows your organization to continue meeting production requirements despite the unexpected work stoppage.
Tips on How to Prevent and Plan for Equipment Downtime
Planning how to stay productive during equipment downtime requires a strategy that emphasizes proactive maintenance. You also need a way to keep track of your service records so you can make smart future decisions about your equipment purchases.
With the right software and training programs, you can stay ahead of equipment breakdowns and prevent costly unplanned downtime. When you partner with the right rental provider, you can quickly secure rental equipment during downtime so you can keep meeting production targets. Here are our top tips on how to plan for and prevent equipment downtime:
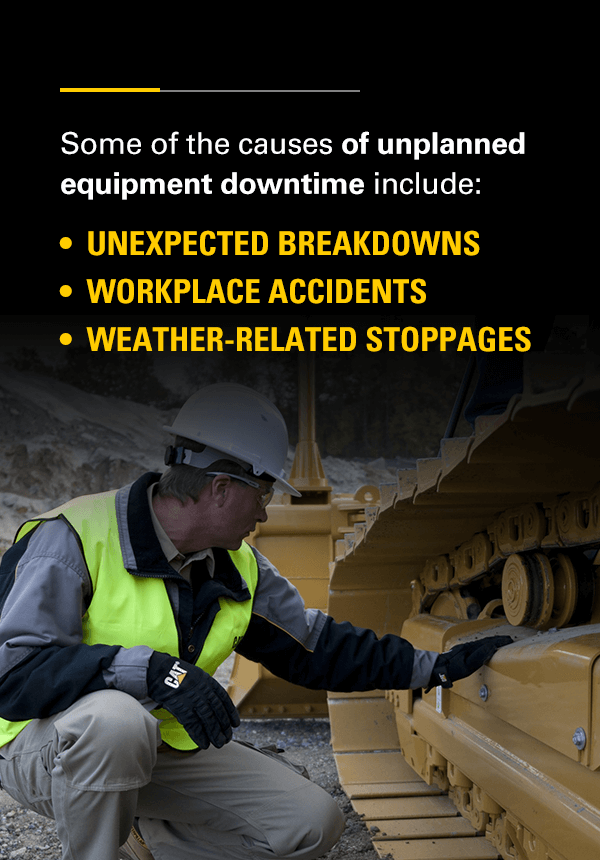
1. Develop a Preventive Maintenance Plan
Since preventive maintenance is your best defense against unplanned downtime, it’s absolutely vital to develop a preventive maintenance program.
A preventive maintenance strategy needs to be based on each machine’s maintenance, repair and servicing needs and the intervals at which maintenance should happen. Each machine needs its own schedule of necessary maintenance activities and intervals, such as number of operating hours or mileage.
A robust strategy will include the scheduled maintenance activities and a contingency plan. Though scheduled maintenance minimizes the risk of unexpected breakdowns, the overall strategy still needs to address what will happen in the event of a breakdown. Include a plan for obtaining rental equipment you can use while the equipment is undergoing servicing in the strategy.
2. Document All Maintenance Activities
What you can measure, you can manage. That’s why having a system for documenting all maintenance activities can help you manage your downtime and make informed decisions about your fleet of equipment.
When you keep thorough records of all maintenance activities, you can start to identify patterns. Perhaps you’ll notice there are a few causes of equipment malfunction. Knowing the most likely causes that lead to downtime allows you to focus your prevention efforts on these factors. If you manage a large fleet of construction equipment, having an effective record-keeping system is all the more important so no machine falls through the cracks.
Documenting your maintenance activities also ensures you can maintain the advantages of your equipment and parts warranties. If you need to make a warranty claim, your record-keeping will help streamline the process.
3. Leverage Software Automation
Preventive maintenance software systems are a vital asset in managing construction equipment and mitigating expensive downtime. Modern software is robust and can collect so much data you almost don’t know what to do with it all. But with maintenance software, you can make intelligent, proactive decisions about your equipment downtime strategy.
Fleet managers can use the data collected about the equipment’s servicing needs to make informed decisions and schedule maintenance activities. In fact, many software programs have features that will automate everything for you — scheduling your maintenance and repair activities and coordinating rotations of other equipment. This drastically reduces the burden on the fleet manager to schedule preventive maintenance so they can focus their efforts on optimizing productivity.
With the help of software automation, managers can coordinate rental equipment that aligns with the scheduled maintenance. Having calendar reminders of upcoming maintenance can alert managers that they need to secure rental equipment well ahead of time.
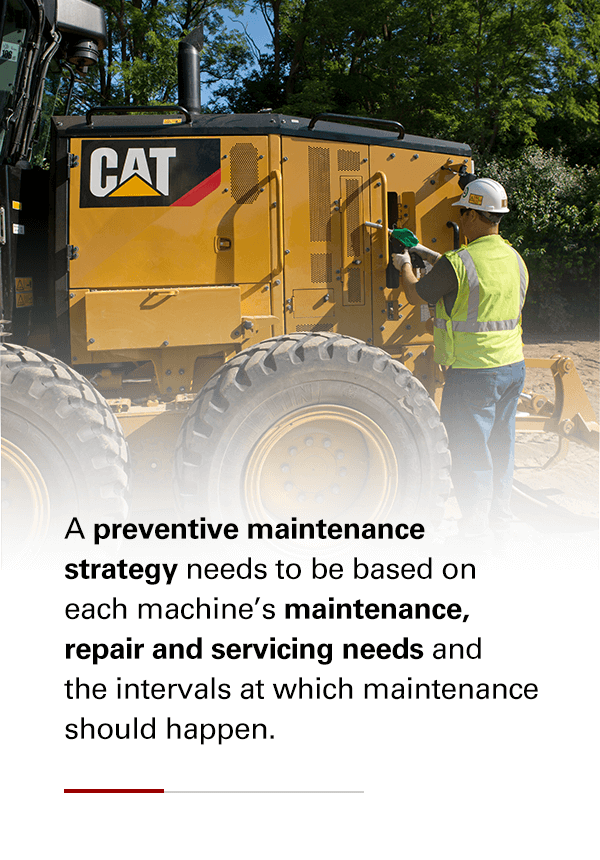
4. Invest in Training
Planning for equipment downtime is a lot easier when your focus is on prevention. While routine maintenance is key to preventing equipment breakdowns, following operating best practices is also crucial to ensuring a long service life. Equipment is designed to be operated for specific purposes and within specific ranges of capacity. Overworking equipment and improperly operating machines can lead to excessive wear and tear on parts and early equipment breakdowns.
Managers can help mitigate downtime, prevent costly and unexpected repairs, and extend the service life of their equipment by investing in proper operator training. Operator training programs and ongoing training should emphasize the importance of safe and proper operation of all equipment.
Operator training programs should also get buy-in on behalf of the operators. Operators who feel ownership over the equipment and are responsible for inspections and reporting issues early on can be a front line defense against equipment downtime.
5. Connect With Local Technicians
Whether you’re a large company managing a massive fleet or you’re a single owner-operator, having technicians readily available to perform routine maintenance and emergency repairs is an asset. Large companies often have in-house technicians at the ready to handle preventive maintenance and quickly get equipment running in an emergency. For smaller organizations, outsourcing servicing needs to local shops is much more cost-effective.
However, even companies with a team of technicians on staff may need third-party shops to help with overflow, particularly for unplanned downtime. Technicians with full workloads will suddenly need to shift their focus to addressing an unexpected breakdown, leaving other current or upcoming maintenance activities aside. The ability to quickly outsource your equipment servicing needs can drastically reduce downtime and keep your production schedule on track.
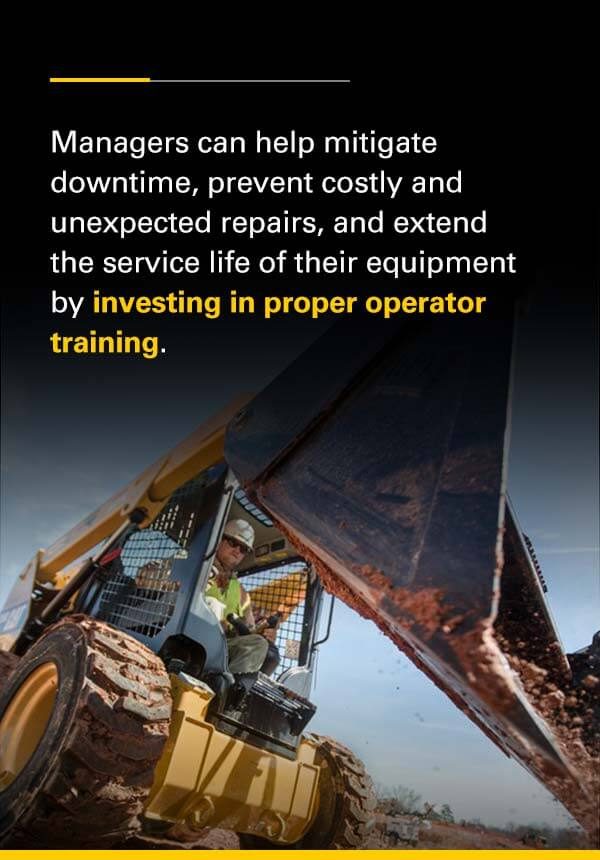
6. Have a Contingency Plan
When planning for downtime, whether for planned or unplanned maintenance, it’s important to have a well-defined and communicated backup plan.
A backup plan should include having spare parts on hand to make emergency repairs. Collecting data on the types of breakdowns and repairs that are most common can help inform your company’s contingency plan and which parts to keep in stock. Having fully stocked fluids and filters should be part of the downtime plan, as these are also routinely checked during inspections.
A contingency plan should also include protocols for accessing replacement equipment to use during the downtime. Downtime due to maintenance and repairs can last a few hours, a few days or several weeks if it requires purchasing a new machine. Having a plan in place for how to obtain equipment in the intermediate can ensure continued productivity.
Managers can include a partnership with a local equipment rental provider as part of their contingency plan to know how to act swiftly when downtime occurs.
7. Partner With a Reliable Rental Provider
When you need backup equipment during planned or unplanned maintenance, it’s critical to have a local equipment rental provider to rely on. Partnering with a reliable rental provider can ensure you line up the correct rental equipment when you need it.
During planned maintenance, you can connect with your rental provider ahead of time to secure the correct model and size of equipment for the duration you need it. Developing a relationship with a rental provider ensures they are familiar with your equipment needs and can help you locate the appropriate equipment when you need it. This is especially crucial in time-sensitive situations, such as when sudden breakdowns occur and you need a replacement machine as soon as possible.
Benefits of Renting From The Cat® Rental Store
Finding and partnering with an equipment rental shop can help you achieve your productivity goals. The right rental provider will have excellent technical expertise and recommend the right machine for the job. They’ll also go above and beyond to locate and secure the right machine and offer you flexible terms that suit your needs.
Your equipment rental provider should offer high levels of customer service and provide well-maintained equipment that you can rely on. For top customer service, equipment expertise and well-maintained machines, choose The Cat® Rental Store to help fill in the gaps during equipment downtime.
Here are some of the benefits of partnering with The Cat Rental Store to help cover your equipment maintenance downtime:
1. Find the Type of Equipment You Need
When you partner with The Cat Rental Store for your equipment rental needs, you can get the right type of equipment for the job, including the correct work tools. Our extensive dealer network allows local equipment specialists to find the right equipment from any of our nearby locations. With over 1,300 locations worldwide, you’re sure to find the right high-performing equipment when you need it.
Whether you need earthmoving equipment, such as excavators, dozers and compact equipment, or specialty equipment, like forest machines and concrete equipment, The Cat Rental Store has what you need.
In addition to supporting your equipment needs during downtime, The Cat Rental Store can provide supplementary equipment to help you increase productivity on any job site. Contact a rental expert at The Cat Rental Store near you today to discuss your equipment needs.
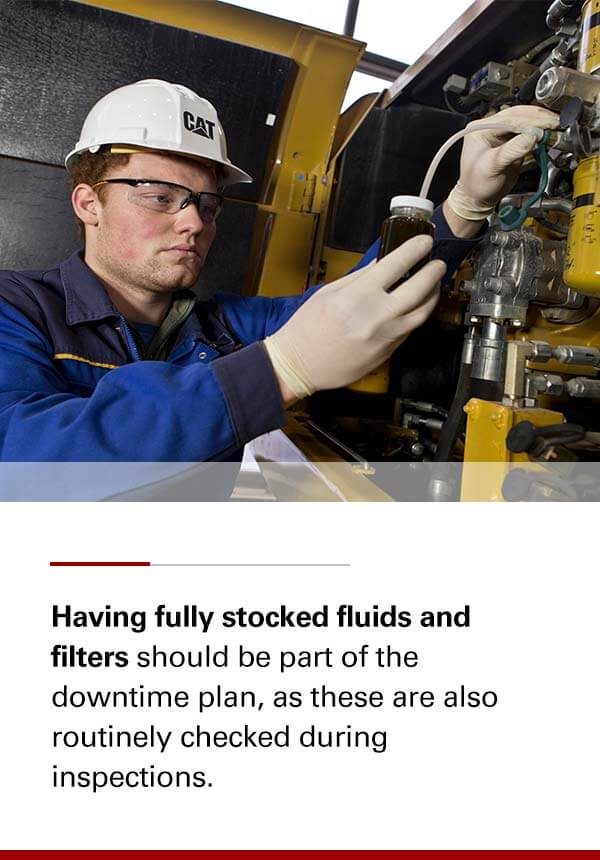
2. Get the Right Size of Equipment
When you need to rent equipment in a pinch, you might be stuck making do with whatever equipment is available, even if it’s not the exact solution you need. This means renting equipment that’s insufficient for the job. Renting equipment that’s either too big or too small for the project can impact productivity and pose safety risks.
Unfortunately, some rental stores will either down-rent or up-rent equipment to their customers to make a sale. Equipment that’s too small for the job is inefficient and causes productivity delays by taking too long to get the job done. Machines that are too big can be overkill, being more difficult to operate and using more fuel than necessary.
When you rent your equipment from The Cat Rental Store, you’ll benefit from our massive dealer network that allows us to locate the right size of equipment for your needs.
3. Choose a Flexible Rental Term
Renting allows you to take on short-term jobs. Depending on the type of maintenance required, your equipment may be out of service for a day, a week or longer. Knowing you can secure high-quality rental equipment in the meantime provides peace of mind.
When you partner with The Cat Rental Store to access rental equipment during downtime, you benefit from convenient and flexible contract terms. Whether you need a daily, weekly or monthly rental, The Cat Rental Store can accommodate. If the maintenance on your equipment takes longer than originally anticipated, you can extend your rental contract so you can stay productive.
Contact The Cat Rental Store near you and talk to your local representatives about our flexible contract terms on all rental equipment.
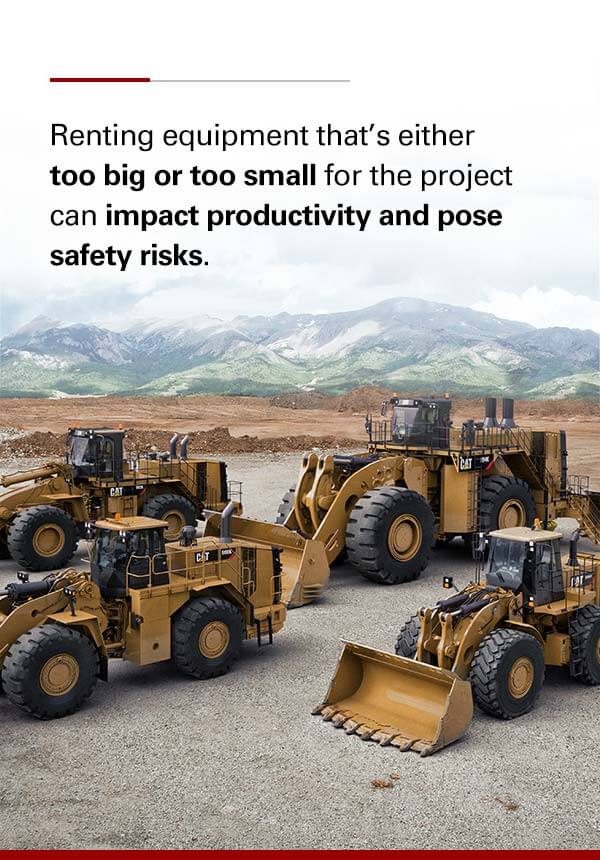
4. Rent High-Quality Equipment
When you rent equipment in a hurry, you may be worried about the quality of the machine and how well it’s been maintained. Renting from The Cat Rental Store eliminates this concern. All Cat rental equipment is serviced and maintained to the highest standards. Our technicians are highly experienced and are experts in Cat equipment. Additionally, our dealers use only Cat genuine parts on all their replacements, ensuring the highest performance possible from your equipment rental.
Our dealers stand by their equipment rentals, and if anything goes wrong, they can provide responsive customer service to help get you up and running.
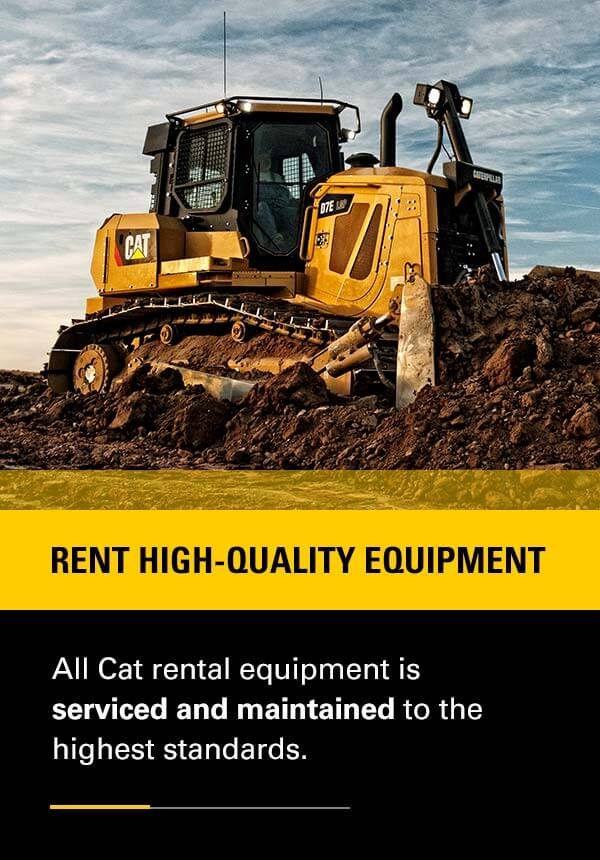
Trust The Cat Rental Store for Support During Equipment Maintenance
Planned and unplanned maintenance require an effective contingency plan that supports your productivity. Having access to high-performing rental equipment during maintenance downtime is crucial to staying productive and profitable. The Cat Rental Store is your solution for high-quality rental equipment to fill in the gaps during maintenance.
With over 1,300 locations worldwide and an extensive inventory of well-maintained equipment, you’ll find what you need at a store near you. Visit The Cat Rental Store near you today to speak to a representative or call us at 1-800-RENT-CAT for 24/7 support.
Find The Cat Rental Store Near You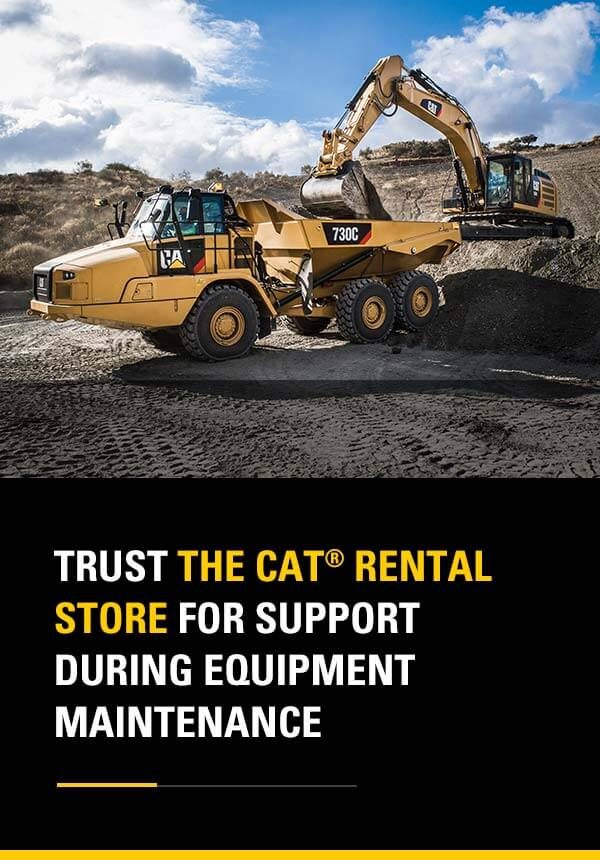